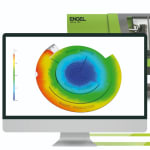
On the occasion of K 2019, Engel announces that it is breaking new ground in the further digitalisation of the injection moulding process in collaboration with Autodesk. The aim is to link the simulation with the real process, in order to be able to better support the plastics processor throughout the complete product life cycle - from product development and tool design through to production. At the K trade fair, which takes place in Dusseldorf from October 16 to 23, exhibition visitors can see for themselves how, with the help of Engel sim link, the results of simulations performed using the Moldflow simulation software from Autodesk can be transferred to the CC300 control of the Engel injection moulding machine - and how process and measurement data can flow back from the machine for use in the simulation.
"Together with Autodesk we are closing the gap between the digital twin of the actual tool and the real injection moulding process", reports Dr. Johannes Kilian, Head of Simulation and Control Engineering at the Product Development Department of Engel Austria. "By creating easily usable connections between the digital and the real world we are facilitating the consistent and mutual utilization of simulation and machine data throughout the complete product life cycle." At the K trade fair both companies are exhibiting a first product, Engel sim link, that will be available to Engel and Autodesk customers next year.
Direct data transfer in both directions
"Up to the present day, many findings obtained from simulating injection moulding processes remain unleveraged on the machine ", is how Kilian describes the motivation behind linking the simulation data with the process data. With Engel sim link, the parameters optimized through simulation can be converted into a setting data record and used directly in the injection moulding machine. The parameters taken from the simulation are adapted to the injection moulding machine intended for the production process. This ensures complete data consistency and dispenses with the time-consuming and error-prone manual input of data into the machine.
Accelerating process optimisation
Another new feature is that process parameters and measurement results can conversely be imported from the injection moulding machine back into Moldflow. This function opens the door to a completely new approach to the analysis and optimisation of the ongoing production process using simulations. Simulation and measurement data can be very easily reconciled and the quality of the simulation improved. Furthermore, with support provided by simulations, unfavourable process settings can be subjected to in-depth analysis and, therefore, adaptations implemented more rapidly and precisely. With the help of sim link, the optimized process data can then be imported to the CC300 machine control unit.
"By linking the simulation with the real production process, injection moulding simulations will in future play a central role throughout the entire product life cycle", explains Kilian. "Simulations accelerate the machine setting, set-up processes and process optimisation, thereby significantly boosting productivity. It is therefore becoming an increasingly affordable competitive advantage for smaller injection moulding companies too."
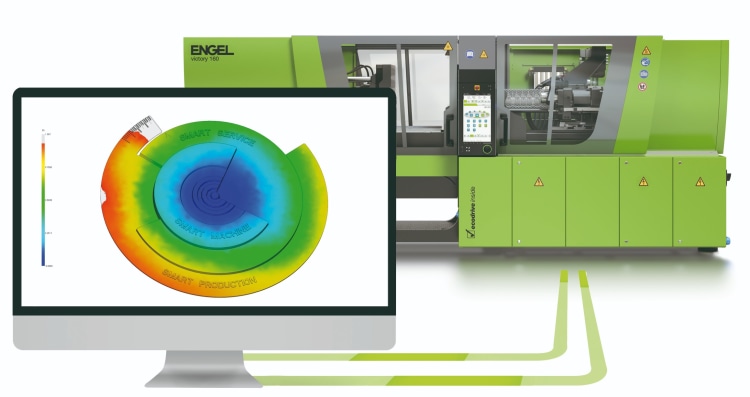