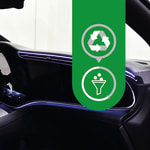
Kraiburg TPE is expanding its portfolio for OEMs and their suppliers, while it significantly contributes to meeting recycling rates and is offering support in reducing the carbon footprint of products for automotive interiors: With a recycling content of up to 38%, interior post-industrial recycled TPE grades provide the automotive market with a reliable and sustainable alternative to virgin material solutions. Customers will also receive the necessary information on the product carbon footprint (PCF) of the TPE.
The automotive industry is using company specific and standardized tests to prove the suitability of materials in automotive interiors meeting customer’s high expectations. Nevertheless, keeping costs under control is always a high priority. To continue to provide ideal support for manufacturers and OEMs in developing new, forward-looking products, Kraiburg TPE is expanding its portfolio to include solutions that are made of up to 38% of recycled raw materials, depending on hardness. A wide hardness range combined with excellent product performance allows an easy integration into the targeted market segment.
The post-industrial recycled raw material used is waste material derived from other companies’ manufacturing process for plastic products. Kraiburg TPE uses it to produce product solutions for sustainable automotive interior applications. Possible applications include anti-slip mats, floor mats, soft components in cup holders, as well as fixation elements. The series is also suitable for other applications requiring a hardness range between 60 and 90 Shore A. Strict OEM requirements for emission and odor are fulfilled and the material can be either combined with polypropylene in co-injection molding applications or used as single soft component solution. In addition, Interior PIR TPE provides good abrasion resistance and excellent flowability combined with low density to keep the part weight at a minimum.
“We’re expanding our product range to include Interior PIR TPE in response to the sustainability issues raised by OEMs. We’re sure our customers will benefit substantially from the option of using TPEs based on recycled raw materials for automotive interiors,” says Matthias Michl, Head of Automotive Application Development at Kraiburg TPE.
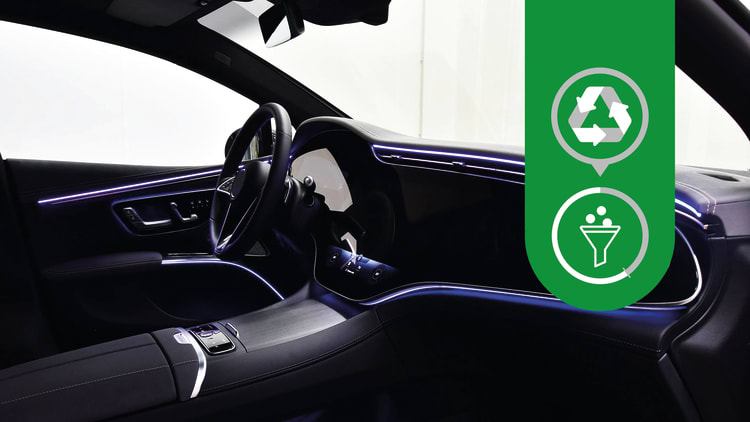
New feature: To support customers in implementing their sustainability projects, Kraiburg TPE is now able to provide the product carbon footprint of compounds for many products. This can lead to a decisive competitive advantage for customers and is part of the TPE manufacturer’s service package. The PCF quantifies the CO2e-footprint – in this case within the system boundaries cradle-to-gate. The global warming potential (GWP) of a product is calculated, indicating how much the product contributes to global warming from raw material extraction to the product manufacture’s gate. Producers require this value to assess the carbon footprint of their components, and ultimately of the whole vehicle. Kraiburg TPE claims full transparency in assessing the PCF and calculates the values according to DIN EN ISO 14067 and DIN EN ISO 14044, following the GHG Protocol. Detailed information on the assessment is provided.
The product is available for customers in the EMEA sales region. Kraiburg TPE is currently working on local solutions for the APAC markets and North America. Matthias Michl sums up this portfolio enhancement by noting that “The new solutions ‘universal PCR TPE’ and ‘Interior PIR TPE’, as well as the option of providing customers with individual PCF values for their purchases, enables us to position ourselves as a reliable and local TPE contact and to offer full service for our products.”