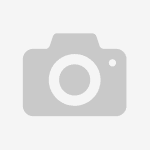
Backed by Eurotherm’s expert engineering support and solutions services, the many systems that make up the Maco Compact Family are derived from a platform of a tightly integrated, application specific programmable logic controller that features built-in diagnostics, process monitoring, advance processing features, and unsurpassed temperature control to ensure production quality is high and budgets to install these systems are kept low.
Eurotherm will also display, for the first time publically, it’s Maco Compact System for the ever popular Van Dorn HT Machine line in which the original control systems are no longer supported by the OEM in the field. This is the totally integrated, expandable control solution for HT owners who want a cost-competitive, reliable solution for maximizing machine potential. The MACO Compact HT System upgrade delivers more precise processing features that can provide better control during the injection molding process, thus improving part quality, saving energy and reducing waste. And, all at a low price that includes installation and startup.
The expandable Maco Compact Control System for injection molding machines features Eurotherm’s Impact II closed loop process control. For improved optimization in closed loop systems, the ImpactII closed loop process control creates a theoretical model of the injection molding process after only a few cycles and uses that model along with hundreds of rules to compensate for any deviations.
Operator interfaces are now available in a sleek, flexible design with a full range of cost-effective HMI’s. Features include, high speed display updates, Ethernet communications, recipe storage ability, online and web browsable RLD diagnostics, Closed Loop Control updates at less than 1.o ms, statistical process control, and large color touch screens.
iPact melt pressure control system with Intellimold revolutionizes injection molding.
Compatible with the Maco Compact Control System, Eurotherm’s iPact melt pressure control system utilizes Intellimold a patented, cutting-edge process that brings real-time, automated closed-loop control to the molding process by actively monitoring and adjusting controls for a steady, even injection. The iPact melt pressure control system with Intellimoldis supported by most original equipment currently used by manufacturers and is adaptable to any molding system as an option item or as an after-market retrofit.
Its unique process control method provides measurements and control of pressure in the cavity in real time. The pressure developments are scanned from two strategically placed pressure transducers from which a single process variable is mathematically derived as a feed back for closed-loop control of injection. With this method and process control, each section of an injection-molded part solidifies in an equal, pressure-balanced and stress-free environment. Intellimold is also capable of measuring and controlling based on temperature developments.
Injection molders will benefit from improved repeatability, reduced waste and cycle times. Intellimold is also a standard option on all Maco Compact Systems for injection molding machines.
Based on the Maco Compact System Platform, featuring operator interfaces that utilize Microsoft CE.net, two reliable Maco controls – the Breeze IIc control system for blow molding and the EM-3c control system for extruders – are Eurotherm’s newest product upgrades for monitoring and maintaining wall thickness control at a nearly 30 percent cost reduction from the previously released PC based versions.
Add the Breeze IIc systemor blow molders to the Compact Control System and you have the latest in parison-only control from Eurotherm. A compact parison board and Compact touch screen display are housed in an optimally sized chassis, eliminating the bulk and costs associated with a separate controller enclosure. Like earlier versions, it can be factory programmed based on user specifications for any machine make or model. With a 100 point parison profile and 100 point velocity pushout control, parison tooling position is updated every 0.1 ms to minimize material usage and improve part quality.
The EM-3c extrusion control system is specifically designed for small extruders but is packed with the features of the popular EM-3 and EM-3c PC based Extrusion Control System. Its operator interface can be used just for extruder temperature and pressure control or complete line control. Manufacturers can save on installation costs due to the system’s preconfigured screens and sequence and standard control system definitions save even more valuable engineering time and expense.
The “Eurotherm Difference”: Solutions design capability.
The Maco Compact System, along with all of Eurotherm’s products and solutions, is backed by industry expertise and ongoing support that is unparalleled by competitors. Eurotherm engineers have an in-depth understanding of industrial applications across multiple markets making the company uniquely qualified to recognize specific challenges and offer tailored solutions to meet any processing need.
Eurotherm engineering services provide complete project management capability from start to finish, including an investigation and full analysis of unique company challenges, design and proposal, full implementation and installation, with lifetime support and training for continued solution enhancement.
Eurotherm is a global supplier of control, measurement and data recording solutions and services to industrial and process customers. The company’s international reputation as a provider of innovative solutions across a broad spectrum of vertical markets is supported by engineering services designed to realize greater benefits to customers’ plant-wide assets.