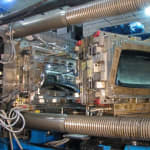
In support of this, Exatec`s Wixom, Mich. global headquarters has expanded its facilities to offer enhanced process development and prototype fulfillment, particularly for large, panoramic roof systems. This investment in new process technologies will enable Exatec to provide automotive customers with advanced product solutions and outstanding technical support.
Exatec, which celebrated its 10th year in business on March 8, is introducing its latest technologies and capabilities, including an upgraded wet coating lab, new Engel injection molding machine, and a unique, full-scale plasma system for continuously coating polycarbonate windows.
The American Plastics Council reports that for each 10 percent reduction in the weight of a car or truck, gas mileage increases by seven percent. Plastics, which offer high performance and durability as well as lighter weight compared to steel, aluminum, and glass, may help lower fuel consumption, according to the Council. In some vehicles, the use of plastics in bumpers, body panels, lighting, fuel tanks, and other components has helped cut total vehicle weight up to 200 pounds.
- Exatec is uniquely positioned to provide the most advanced range of coating solutions with Lexan polycarbonate resins for automotive glazing applications - said John Madej, president of Exatec LLC. - This expansion to our Michigan facility enables Exatec to serve as a one-stop shop for the most advanced automotive glazing solutions available - he adds.
New capabilities for panoramic roof glazing
Automotive components such as large panoramic roofs benefit greatly from the use of PC glazing. The addition of a panoramic roof typically doubles the weight above the beltline vs. a traditional roof, requiring enhanced vehicle suspensions and other compensatory engineering for the vehicle to maintain its performance.
Exatec operates a global technology development center located in Wixom, Mich. Key technology development includes 2K molding, silicone hardcoat development, and application methods; PECVD coatings to enhance weathering and abrasion resistance; and development of enabling technologies including defrosters, fractal antennas, and electroluminescence.
The Wixom facility offers injection compression molding with two colors; a wet coating lab for research and prototype programs in a clean room environment; the only full-scale plasma coating system; large (up to 52 in x 98 in) flat-screen printing machine, and a full testing laboratory for PC glazing.
Exatec works with several material suppliers, including Engel for 2K injection compression molding machines, InGlass for tooling suitable for PC glazing applications, and Momentive Performance Materials for silicone hardcoats.