Composites aid the cause
Continental Structural Plastics Inc. (CSP), along with its Japanese parent company Teijin Ltd., recently unveiled an advanced, multi-material EV battery enclosure that can be molded in any number of CSP’s proprietary composite formulations, as well as a new honeycomb Class A panel technology.
CSP’s multi-material electric vehicle battery enclosure is 15% lighter than a steel battery box. Although it is equal in weight to an aluminum enclosure, CSP says this enclosure offers better temperature resistance than aluminum, especially when used with its own, proprietary phenolic resin system.
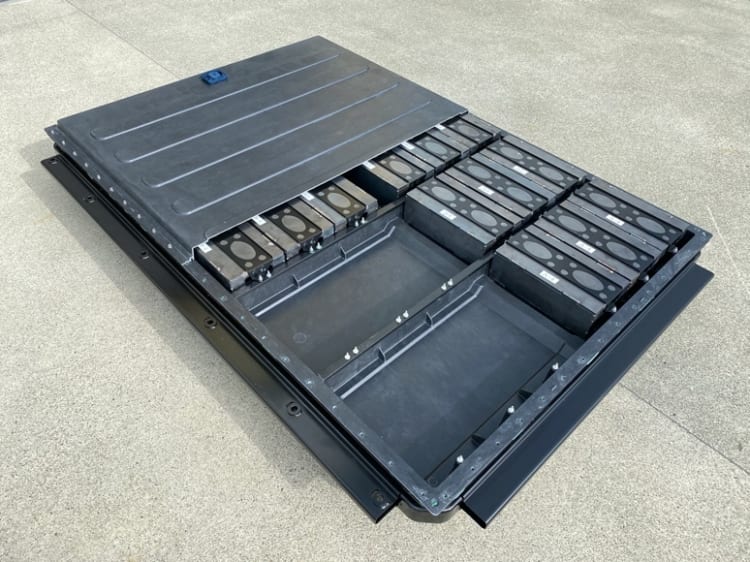
CSP’s multi-material EV battery enclosure is 15% lighter than a steel battery box. (Image courtesy of Continental Structural Plastics)
CSP says it currently is in development and production of more than 34 different electric vehicle battery box covers in both the U.S. and China.
Separately, the company has developed a new honeycomb manufacturing process that produces ultra-lightweight Class A panels. Considered a “sandwich” composite, these panels use a lightweight, honeycomb core, clad with natural fiber, glass fiber, or carbon fiber skins that are wetted with polyurethane resin. This process enables the molding of complex shapes and sharp edges, and results in panels that offer very high stiffness at a very low weight.
Radar-absorbing compounds
Sabic has unveiled two new, radar-absorbing LNP™ STAT-KON™ compounds for automotive radar sensors, significantly expanding its portfolio of these specialty materials. The new grades –– based on polybutylene terephthalate (PBT) resin –– may be used for integration with radomes manufactured using PBT material, which can provide superior resistance to automotive chemicals.
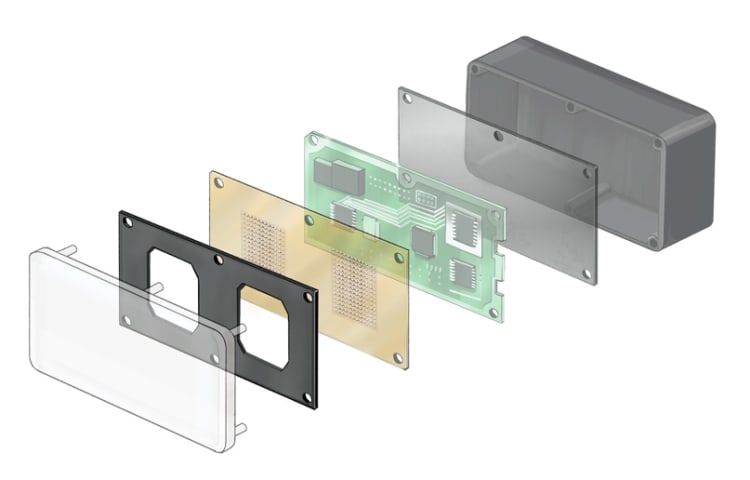
This exploded diagram is of a typical automotive radar sensor with all the components faded, except the radar-absorbing plate, which is second component from the left. (Image courtesy of SABIC)
They complement and extend SABIC’s existing radar-absorbing LNP STAT-KON compounds, which are based on polyetherimide (PEI) resin for withstanding higher processing temperatures or on polycarbonate (PC) resin for general applications that require high durability and a balance of physical properties. The high radio frequency (RF) absorption of these compounds can help increase detection range and improve signal resolution.
Radar sensors are widely used in advanced driver assistance systems (ADAS), where they provide capabilities such as blind spot detection, collision avoidance, automatic braking and traffic alerts. Radar-absorbing materials (RAM) are used to shield the field of radar wave transmission and attenuate side waves that can cause ghost images or trigger false actions or alarms.
BASF’s mobile charger
Germany’s BASF, meanwhile, also is striving to apply its materials to creative solutions related to the EV sectors. The company says it partnered with two Japanese firms –– ZMP Inc. and B & Plus –– to create a conceptual autonomous wireless charger that aims to meet increasing demand for charging infrastructure solutions. BASF says its Ultradur polybutylene terephthalate (PBT) and Ultramid polyamide (PA) are used in the mobile charger’s radar housing, lidar sensors, protective films, and other electrical components and devices.
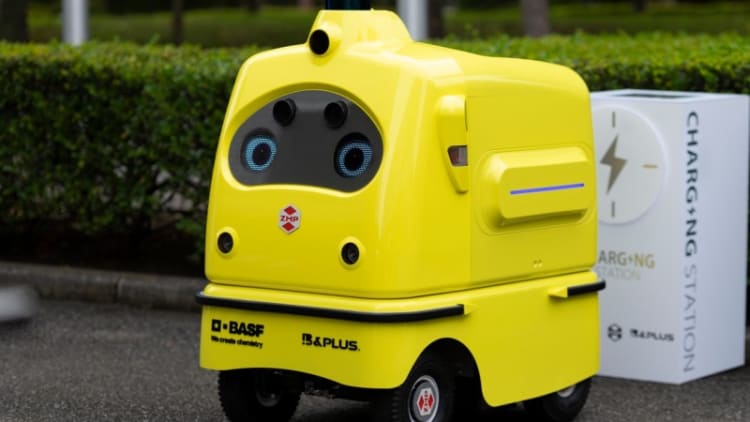
BASF sees its MobiPower concept as an autonomous, wireless charging solution for future electric vehicles. (Image courtesy of BASF)
More than 75 billion connected devices — such as phones and electric vehicles — are expected.
to need charging by 2025. Dr. Hisashi Taniguchi, founder and CEO, ZMP Inc., said: “MobiPower enables us to meet this market demand, with a convenient charging solution that is robust enough to house sophisticated components and sensors combining 5G, IoT, and AI capabilities, as well as being durable enough for the outdoors. BASF expanded my creativity and the possibility of our robots.”
See more of these types of material innovations at Chinaplas 2021 in Shenzhen next April 13-16. Come see first-hand some of the amazing technologies that are helping to enable the vehicles of tomorrow.