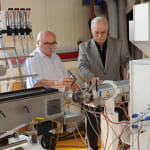
- At the beginning there was the demand by Soplar to increase the throughput on the blow moulding machines for bottles by between 30 and 50 percent with the use of new extruders.” As a result, the academically qualified engineer Eberhard Grünschloß developed a new single screw extruder which he called
Helibar.
In mid-1999, Extrudex Kunststoffmaschinen GmbH, in Mühlacker, Germany, patented this technology. Since then, the system has been continuously improved, refined, tested, and declared a ‘runner’ - not with regard to RPM, but certainly when it comes to energy efficiency, economy, reliability, endurance, and longevity. “Even after three years of continuous production, REHAU (as international global polymer processing company supplying products to the construction, automotive, and industry sectors) has not been able to discover discernible wear in the Helibar processing unit”, Eberhard Grünschloß quotes the core clause from a paper published on the subject.
The Helibar energy consumption can be lower – between 10 and 60 percent – than usual because of the reduced cooling demand and the smaller size at equal output. Tests have revealed: a 10 percent improved energy saving rate compared with state-of-the-art extruders of grooved bushing design, 20 percent more efficient compared with older machines – achieved by retrofitting the process unit (screw/cylinder), and keeping the existing gear system/motor, up to 60 percent better when replacing the complete unit i.e. a 90 screw diameter (OD) extruder with a 60 OD Helibar.
Helmut Wahl, CEO of Extrudex, attributes the advantage to the fact that the ‘lack’ of wear – even when processing aggressive raw materials containing additives and/or masterbatch – is due to the low pressure within the feed section of the extruder: “In addition, this factor is equally responsible for the low energy requirement, aided by lower friction heat and a reduced cooling requirement, not forgetting the option of complete cylinder insulation”, adds Wahl.
Consequently, the heating capacity is utilized to a much greater extent with Helibar, achievable by the direct heat transfer from the electric heaters to the polymer: “because the cylinder is grooved, because the developing melt is immediately being pressed into the grooves, and because the melt layer between the hot cylinder and the cold solid material can thus be kept much thinner. Subsequently, the heat transfer between the hot cylinder and the cold solid material is considerably improved and the solid material can be melted much faster. At the same time, much improved material feeding is achieved, as the shear stress between the cylinder and the cold polymer increases – similar, for instance, to the displacement of water by the tread on car tyres”, as Grünschloß explains the physics in context.