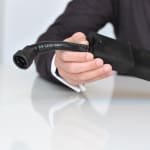
The fuel vapor separator is an important element of the complete fuel delivery system in road vehicles. It separates vapors from liquid fuel coming out from the fuel tank, and prevents the liquid fuel reaching - and contaminating - the fuel vapor canister. This prevents the evaporating fumes from reaching the atmosphere while also maintaining proper fuel tank pressures.
While fuel lines themselves have a coextruded outer cover in a flame retardant thermoplastic, fuel vapor separators are most often still made from a non-flame-retardant polyamide. Dytech Dynamic Fluid Technologies, based just outside Turin, Italy, now part of Tokai Rubber Industries Ltd group, develops and supplies fuel delivery components and systems for many of the world’s leading automotive companies. Dytech chose the innovative halogen-free flame retardant EcoPaXX to meet increasing fire safety requirements as well as a wide range of other demanding requirements for the application.
EcoPaXX is highly resistant and impermeable to conventional gasoline fuel (E10) as well as to the more sustainable E85 fuel. In the SHED (Sealed Housing for Evaporative Determination) test, EcoPaXX fuel vapor separators showed a very low permeation level for E10, of 0.002 grams/24 h. EcoPaXX Q-KGS6 has a UL 94 V-0 flammability rating at 0.7 mm.
The high thermal stability of EcoPaXX is demonstrated by its Maximum Continuous Use Temperature of 175°C. This engineering plastic also has very good dimensional stability (proven by short term aging at 100°C), and outperforms current materials used in low temperature impact tests carried out at -30°C. EcoPaXX also passed tube extraction and impact tests after thermal and fuel aging, as well as fatigue resistance.
EcoPaXX has, in addition to its unique technical performance, an extra advantage in that polyamide 410 is 70% derived from renewable resources and is certified Carbon Neutral from cradle to gate.
"We have been very impressed by the performance we have obtained from the new EcoPaXX fuel vapor separators," says Mario Zasa, Research & Development at Dytech. "Our customers make some of the most prestigious cars on the road, and they call for top quality solutions from their suppliers. Working with DSM, we have succeeded again in meeting their demands."
DSM engineering plastics are increasingly used in various elements of automotive and non-automotive fuel systems. For example, another grade of EcoPaXX, Q-HG6, has been tested successfully in automotive fuel line quick couplings, and Akulon Fuel Lock, a special grade of polyamide 6 for injection and blow-molding applications, provides outstanding resistance to permeation without the need for additives or post-molding treatments in such products as CNG (Compressed Natural Gas) tanks. DSM’s strong competence in polymer physics and chemistry has led it to a strong position in the development of numerous materials with important features required by its partners in automotive and other industries, whether they are high flame retardance and high barrier as in this case, or other key mechanical, chemical or electrical properties. This latest application is one more demonstration of how DSM applies its bright science to create brighter living.