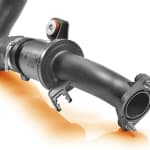
Automotive Tier1 supplier Hutchinson, selected Stanyl Diablo OCD2100 for the Turbo charge air duct resonator on the Alfa Giulietta 1.6 L Multijet 105 Hp Euro 5 Turbo Diesel engine. The resonator acts to dampen noise in the charge air system.
According to Maurizio Servetti, responsible for Group Materials Labs Plastic unit of
Fiat Group , this is one of the first Turbo resonator of its kind made in plastic for a FIAT Group Automobiles engine platform: “At Fiat we are committed to increasing the level of acoustic comfort , while at the same time protecting the environment by decreasing noise and increasing fuel economy. We found that thanks to its unique long time high heat ageing performance, Stanyl Diablo OCD2100 was the only material we could approve for temperatures above 200°C for 3000 hours.”
Stanyl Diablo OCD2100 is the first grade of a next generation family of Stanyl PA46 grades that offer a revolutionary improvement in long term thermal stability. This technology, developed and patented by DSM, extends the functional life of components well beyond the limits of other high temperature polyamides. By limiting thermal oxidative breakdown, Stanyl Diablo withstands more than 5,000 hours temperature exposure up to 220°C with less than 15% loss in mechanical properties.
Hutchinson technical team says: “Thanks to the combination of superior mechanical and fatigue properties at very high temperatures and its welding retention, Stanyl Diablo OCD 2100 was one of few engineering plastic that could meet the Fiat technical requirements while at the same time offering a cost advantage compared to current metal solutions.”
Ton Vet , Application Development Manager for DSM Engineering Plastics adds: “Stanyl Diablo OCD2100 outperforms current high heat resins on high temperature stability, but also on weldability, weld strength and the weld’s long term heat stability. Part design and function can be reached more easily and, more importantly, under-the-bonnet part reliability can be guaranteed for the lifetime required.”
DSM’s Stanyl materials are easy to process. During injection molding, tool temperatures of 80°C and melt temperatures around 300°C are normally used. Short cycle times can be achieved to reduce system costs.