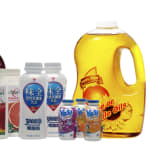
Bekum, machine builder and specialist for extrusion blow moulded packaging, will be at the exhibition Interpack, at booth B32 in hall 13 and inform about packaging trends and production innovations. The focus is on the processing of recycling materials, calcium carbonate (chalk) and newly developed PET materials, the processing of which Bekum specializes in as an industry leader. With the “Concept 808” machine study presented at the K 2019 trade fair, Bekum heralds the future of the extrusion blow moulding machine with more energy-efficient extrusion and very fast production changes for the up-to-date production of packaging.
Circular Economy – Material sayings with tri-extrusion technology
The ability to open up a range of applications for processed plastic waste is one of the key tasks that needs to be addressed as we move towards a circular economy. The ability to contribute to the implementation of practical circular economy solutions is one of Bekum’s primary concerns. For a number of years now, Bekum has been committed to the circular economy and has been delivering solutions for the cost-effective use of correctly sorted PE or PP post-consumer recycled materials. That is why Bekum was presenting 3-layer bottle production that included the processing of recycled materials as early as at the 2007 K Trade Fair. By using Bekum’s tri-extrusion technology and three-layer heads, it is possible to create resource-efficient blow-moulded containers. During this three-layer process, the recycled material (PCR) is embedded in the middle regrind layer between thin-walled inner and outer layers, which are manufactured from virgin materials. Of particular ecological concern is the ability to achievethe highest possible PCR loading in the middle regrind layer, taking into account the geometry of the moulded part, in order to reduce the overall consumption of new plastics within the production cycle.
The ability to guarantee that the plastics have been correctly sorted is crucial for this. It is only possible to easily recycle the three-layer product at the end of its useful life and reintroduce it into the circular economy if the inner layer, the outer later and the regrind layer are all made of the same material.
In addition, the use of PCR in the middle layer can often bring about a reduction in the cost of manufacturing containers.
Clear PET handleware packaging
Over the past several years, Bekum has optimized our PET processing technology, through extensive extrusion system developments, machine optimizations and overall PET process know-how gains. The extrusion blow moulding of PET bottles integrating a true flowthrough handle identifiable as #1 recyclable PET has long been a packaging goal for consumer products groups. By year’s end, a total of sixteen (16) Bekum HYBLOW 407D and HYBLOW 607D machines will be engaged in round-the-clock, fully automated production of handled bottles in fully #1 recyclable PET – this increases the total installation for this application to 40 machines in North America.
Extensive extruder and feedscrew development has been performed by Bekum to address the primary challenges of extruding high viscosity PET. The shear sensitivity of PET at higher throughput rates can drastically increase stock temperature and reduce parison hang strength. Also regrind presents a problem due to the differences in melting characteristics and bulk density of bottle/flash flake. Bekum’s Extrusion System development results in consistent PET material throughput at acceptable stock temperatures when running up to 50% process regrind.
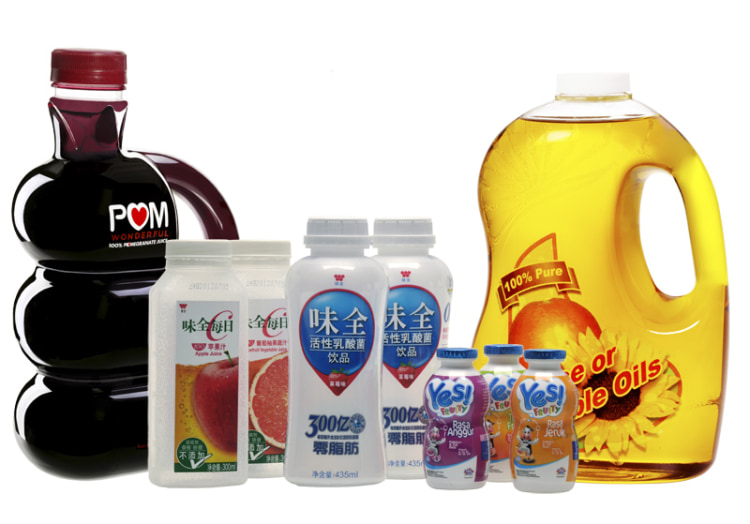
High-output and Energy-efficient Extrusion Package
Extruders are the main consumers of energy in any extrusion blow moulding machine. Bekum places particular importance on energy efficiency when developing extruders. A well-tuned high-output extrusion system essentially ensures product quality. The new generation of high-output extruders HiPEx 36D of the future packaging machine line distinguish themselves through processability, high maximum throughput, and excellent melt homogeneity. Bekum use highly energy efficient IE5 extruder motors and drives, which are important to achieve high energy efficiency.
Fast production changes – 15 minutes for a mould change
Reductions in the size of production runs and ever-present cost pressures require more frequent production changeovers and demand increasing flexibility from blow moulding machines.
The changing of blow moulds and, in particular, of multiple blow pins is complex and set-up procedures have a direct impact on the productivity of the plant. Where articles being produced are changed often, a quick and reliable method that allows blow moulds and tools to be changed as quickly as possible using magnetic clamping technology and without the need for any additional adjustments is worth its weight in gold. The magnetic quick-change system for blow moulding machines, available for the first time from Bekum, allows moulds to be changed in just 15 minutes per clamping unit – without the need for tools or special mould carriages. An integrated roller table, which is required in order to remove the moulds, only takes up a small amount of space. Moulds are inserted into and removed from the front of the machine, which means that there is no need to leave space at the sides of the machine for this purpose, allowing more machines to fit into the production area. Moulds can be transported using either a fork lift or a crane. There is no need to use a special mould carriage. All that is required is a magnetic mould platen back to be able to integrate existing moulds into the system, usually simply and cost-effectively. Electrical energy is only required for the clamping system during magnetization and demagnetization. The clamping function is guaranteed in the event of a power outage.
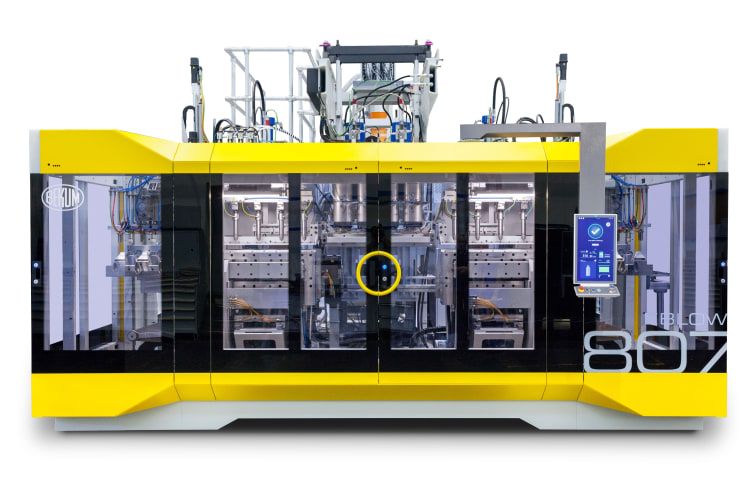