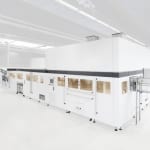
The public demand for more sustainability is growing stronger. As a result the industry is increasingly concentrating on the recyclability of PET bottles. However, this type of packaging often contains composite materials which considerably hinder simple, pure-grade recycling. KHS’ FreshSafe PET technology offers the beverage and food industries a unique alternative. A wafer-thin protective layer of chemically pure glass on the inside wall of the PET container combines product protection with full bottle-to-bottle recycling. This has now been officially acknowledged by North America’s Association of Plastic Recyclers (APR): this recognizes PET bottles coated using Plasmax barrier technology as meeting or exceeding APR’s most stringent Critical Guidance criteria for recyclability.
''Plastics are being subjected to increasingly critical questioning. People want more sustainable solutions from the industry,'' says Jon Elward, head of Plastic Packaging at KHS USA, Inc. ''The demand for clean recycling systems in particular is steadily gaining in significance.'' The gradual ousting of mixed material PET bottles which are hard to recycle is progressively opening up the market to packaging systems which are easy to recycle. In this context KHS’ FreshSafe PET technology provides a suitable alternative and has now been classified as meeting APR’s most stringent Critical Guidance criteria for recycling. The wafer-thin glass coating applied to the inside wall of the bottle is washed off during the recycling process, producing pure PET. ''We’ve fully satisfied the strict specifications and critical demands of the recognition process,'' states Elward. ''This again proves that FreshSafe PET is the only sustainable technology on the market and a reference for the recyclability of PET bottles without composite materials.'' With it sensitive products such as juice, wine, sauce and liquid food are protected from oxidation and carbonated beverages from carbon dioxide loss. Furthermore, compared to standard composite materials the coating process provides a much better barrier quality and ensures much longer product shelf lives.
APR aims to improve recycling quality of PET bottles
''This technology considerably facilitates recycling and at the same time improves the barrier properties of PET bottles,'' confirms Steve Alexander, executive director of the APR. Through its recognition program the organization aims to improve the recycling quality of plastic bottles. According to Elward, interest among bottlers is growing in the system which has already been tried and tested many times over on the market. ''There is an increasing demand for sustainable packaging.'' With the recognition issued by the APR bottlers and recyclers can be more confident the technology supports the American PET recycling market. ''This is a significant step in further establishing this technology,'' Elward believes.
The EPBP also gives FreshSafe PET top marks. In its design guidelines the platform rates the materials used with regard to their recyclability using a traffic light system. The SiOx coating is described as being the only fully compatible barrier technology.
KHS calculates individual TCO
Beverage producers of course incur additional overheads when they invest in FreshSafe PET yet these quickly pay off as the overall operating costs at the plant are reduced. When they use this system bottlers can switch to less expensive standard PET preforms, relieving them of the obligation to source preforms from a specific manufacturer. KHS offers plant operators an individual consideration of the total costs accrued when using its barrier coating technology. ''Measured against the huge benefit of additional product protection and longer product shelf lives in particular, the costs per bottle are actually lower than when conventional composite materials are used,'' smiles Elward.
Source: KHS