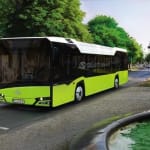
In 2021, the market for heat-resistant polymers is expected to reach USD 16.67 billion – an almost 40 % growth from 2016. Combine this with a biopolymers market that will grow by 12 % each year within the same timeframe, and a societal shift towards a circular economy, and you’ve got a high-potential market looming in front of you.
It is probably this observation that led to the initiation of the EU-funded BRIGIT project in August 2012. Bringing together 16 partners from 12 countries, the project aimed to develop a cost-effective, environment-friendly, continuous process to produce biopolymers from the sugar byproducts generated during sulfite pulping. Every year, nearly 0.5 million tonnes of these sugars are destroyed to avoid altering the quality of highly-demanded lignosulfonates.
Besides the unique use of this waste stream, BRIGIT innovates by integrating its process with the existing pulping industrial operation. This potentially allows for an overall reduction in resource consumption and greenhouse gas emissions, along with a dramatic reduction of operational costs due to the use of non-sterile steps, the absence of intermediate discontinuous bioreactors and the avoidance of waste transport.
‘Our goal was to produce polyhydroxybutyrate (PHB) and Poly-Butylene-Succinate (PBS) from this lignocelullosic sugar feedstock. We do that by using an “in-situ” fermentation process and new fermentation culture technology that prevents any alteration of the quality of current lignosulfonates,’ explains Miguel Ángel Valera, coordinator of the project for Aimplas in Spain.
High-tech products for the transport industry
These two types of biopolymers were chosen for good reason: PHB has good thermal and mechanical properties, and PBS is used to improve the resilience and processability of PHB. By combining the two, BRIGIT partners can build composites for high-tech fire-resistant applications, mainly for the transport sector.‘By combining these biopolymers with natural fabrics (flax, hemp etc.), we provide an alternative to 3D sandwich panels made from thermoset resins reinforced with continuous glass fibres,’ Valera explains. ‘The new panels will be recyclable and lighter. They present broad processing windows, high production capacity (using a continuous compression moulding process) and low embodied energy in comparison with current panels.’
Thanks to participation of FIAT and SOLARIS, the panels were extensively tested and proved to have similar mechanical properties to petrol-based ones. Yet, their higher weight and cost are posing problems which the consortium is still trying to overcome: ‘The first issue will be solved by optimising the panel structure and using few amounts of glass fibres. However, the second one is more complex due to the comparatively low cost of petrol-based resins and the need of large-scale production facilities to be cost competitive. Our technology readiness level (TRL) was unfortunately too low for real market implementation at this stage,’ Valera says.
Besides these 3D panels, Valera and his team have identified various products with high commercial potential: these include PHB and PBS biopolymers grades suitable for cast-sheet extrusion, flame retardants based on chemical modified lignosulfonates, and sandwich panel production by continuous compression moulding.
Moving forward
Nevertheless, the team is still hopeful that it will eventually be able to deliver a low cost, inhibitors-free, and homogeneous source of sugars to produce the target polymers and additives at a competitive cost within the next few years.Most recently, scientific consultancy Daren Labs has shown interested in scaling up the production of chemically-modified lignosulfonates as a flame retardant for biopolyesters and other petrol based plastics. It has requested EU support under the SME instrument. Meanwhile, other project partners are looking for opportunities in DEMO projects to increase the TRL of the technology and complete the optimisation of the fermentation process for alternative sulfite pulping companies.
Source: Cordis
photo: Solaris