arburgXworld: All of Arburg’s knowledge in a single app
The many features of the arburgXworld customer portal, and in particular the new “Ask ARBURG” premium app, also met with a great response. The app offers decades of Arburg experience paired with artificial intelligence (AI) and is being continuously expanded. Working like the well-known large language model ChatGTP, it is being continuously populated with new content and will in future answer any questions relating to Arburg’s range of products and services, including injection moulding, additive manufacturing, automation, digital products, training and service.
The Arburg host computer system, which is now available in the new ALS 8.0 version, is the central MES for plastics processors, enabling them to digitally plan and control their entire production process and increase OEE (overall equipment effectiveness) by an average of around 26 per cent, as a representative survey has shown. Those also interested in the Arburg Remote Service, available “Ready2Go” machines or retrofits were in exactly the right place in the service area.
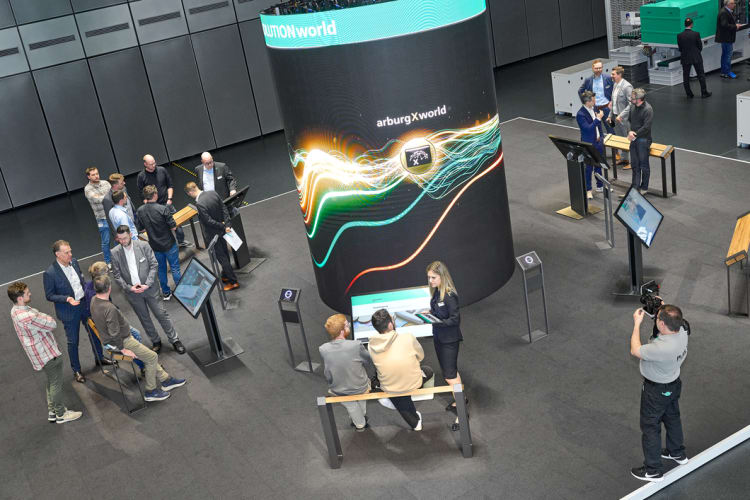
40 exhibits: Expertise and wide variety of applications
Arburg demonstrated its expertise in plastics processing with over 40 other exhibits. Application highlights included:
- The new Mantara lightweight construction process, which combines physical foaming with injection compression moulding and expansion stroke. The result is up to 60 per cent less clamping force and 30 per cent lighter parts with a homogeneous foam structure.
- High-quality IMD film technology for trims and control panels, for example. An electric Allrounder 820 A, which produced a “wallbox” demonstrator, showed how high-quality surfaces can be customised using this technology.
- The processing of Systalen® post-consumer recyclate (PCR). An electric Allrounder 720 A, equipped with the “aXw Control RecyclatePilot”, processed the PCR made from 100 per cent household waste into thin-walled flower pots.
- The production of 70,000 LSR sealing elements per hour was demonstrated by an electric Allrounder 520 A with a 256-cavity mould from Rico.
- The two-component injection moulding of food-safe spatulas made of PCB and LSR with an Allrounder More 2000.
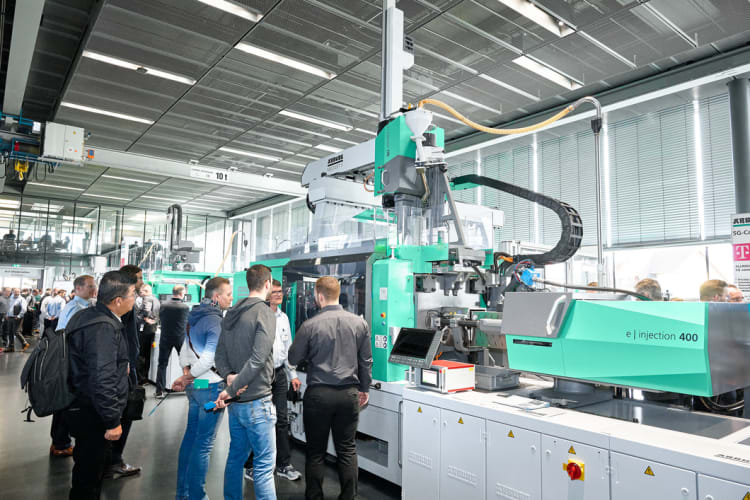
“30 years of Automation + Turnkey”
In addition to machine technology, Arburg has been offering its own automation and turnkey solutions for exactly 30 years, and a number of current customer projects related to this were once again on display at the Technology Days 2024. One example was an electric Allrounder 370 A with a shortened linear robotic system mounted inside the machine guard, so that the footprint was not increased. An electric two-component Allrounder 520 A with a clean air module above the clamping unit was automated with a horizontally engaging Yaskawa six-axis robot positioned between the two injection units in the L-position to save space. Another particularly innovative application was the fully automated production of cartridges with IML labels made from mono-material on a hybrid Allrounder 820 H.
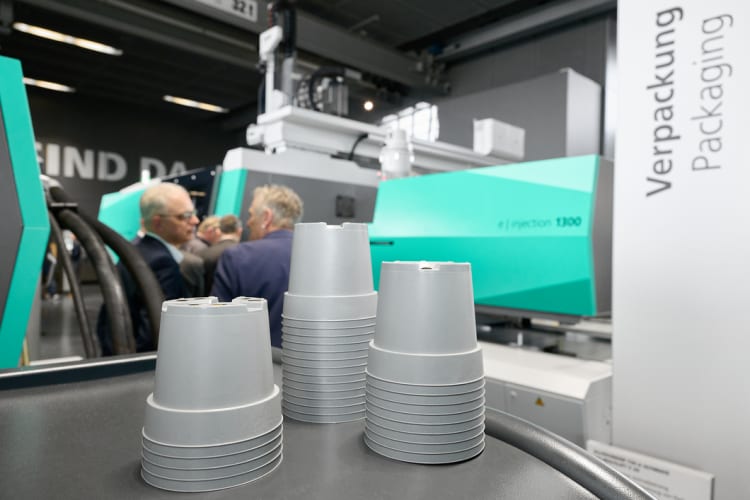
3D-printed operating equipment and fibre-reinforced components
With Freeformers and 3D printers from the TiQ and LiQ series, ARBURGadditive offers a suitable solution for practically every requirement. At the Technology Days 2024, visitors were shown the additive manufacturing of carbon fibre-reinforced components made of PPS with a TiQ 2 and the processing of LSR with an LiQ 5, for example, alongside high-temperature applications and multi-material combinations with the Freeformer 750-3X. The additive manufacturing of spare parts, grippers and operating equipment based on 3D scans is of particular interest to injection moulding plants.