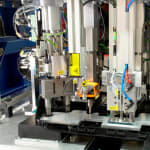
The conventional concept of function integration originates from design theory pursuing the goal of covering as many technical functions as possible with as few components as possible. Today, it is an indispensable principle of modern manufacturing processes: several process steps are combined in one production unit to improve the added value potential. There is no need to interrupt the process chain; this contributes to reducing unit costs and increasing production safety.
Implemented process interlinking with multi-head machines
Large, complex plastic parts are welded in multi-head machines. Integration of auxiliary functions has long been common practice, with obvious advantages: Plastic components with sensitive surfaces only have to be handled once when being inserted into the suitable fixture. Prevention of unnecessary part handling saves time and protects the product.Function integration in multi-head welding machine for automobile engine cover: entire tool change kit
In the example shown, a multi-part engine cover is assembled and welded to the sound insulation mat. The work space comprises a large number of auxiliary functions. These include mechanical pressing-in of rubber dampers and scanning for correct fit, printing of a barcode label and verification of legibility, as well as permanent engraving of the component.
Details of function integration: Ultrasonic welding(1), scratch embossing equipment (2), mechanical press-in unit (3) and sensors