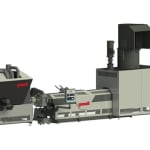
Extrusion technology
MRS-Technology combined with the brand new JUMP system for reprocessing PET waste to high value productsQuick and cost-efficient reprocessing of PET industrial and post-consumer waste
The Gneuss Processing Unit (GPU) has been available for several years now and has proven itself on the reprocessing of bulky PET waste such as post-consumer bottle flake and industrial waste from fibre and film manufacture. This Gneuss Processing Unit consists of the Gneuss MRS extruder with its unmatched devolatilisation and decontamination performance together with the highly-efficient Gneuss Rotary Disc melt filtration systems and the Gneuss Online Viscometer for intelligent dynamic viscosity control, monitoring and logging.
Since the last K, Gneuss has continued with its intensive development programme so that the MRS extruder represents an extremely robust, rugged and reliable system especially tailored for recycling applications. A further development is the extension of the venting system with several openings in the barrel. Depending on the application, these additional openings can be in form of several openings in the MRS section of the barrel or venting ports in the barrel of the plasticising section.
Additionally, Gneuss has developed the new Jump system. This is installed directly downstream of the Gneuss Processing Unit and thanks to its ingenious process ensures an accurate and controllable IV boost of the PET by up to 0,3 in the melt phase. The Jump system is a compact, quick and efficient alternative to conventional SSP (solid state) systems and enables direct reintroduction of the polymer into the production process without the need to remelt the PET.
Depending on its properties, industrial waste is first fed through a shredder or a knife mill until the size is reduced so that it can be fed into the extruder. This can mean either compaction of the size reduced waste or a crammer feeder fitted directly to the extruder.
The first important processing stage: melt decontamination takes place in the extruder. With its enormous devolatilisation capacity, the MRS extruder can process PET waste with high residual moisture levels and/or contamination (such as spin finish oils) without the need for any pretreatment of the waste. In the Multi Rotation (MRS) section of the extruder a huge polymer surface area and extremely rapid surface exchange rate under vacuum ensure that all these volatile contaminants are reliably extracted.
Solid contamination is extracted with the fully-automatic and process-constant Gneuss Rotary Melt Filtration System. With filtration finenesses of down to 20 μm and below, a pure and particle - free polymer melt is guaranteed.
Subsequently, the purified and homogenised polymer is fed by means of a melt pump into the Jump, where the second important stage of the process takes place. Here, too a large surface area of the polymer melt and optimum residence time of the polymer under vacuum are decisive factors. The polymer melt is kept under vacuum as it passes over slowly rotating elements.
Gneuss industrial waste recycling line as to be shown at the K. MRS 90i extruder equipped with dosing feeder and crammer-feeder system, Rotary Filtration System RSFgenius, Online Viscometer VIS and Jump system.