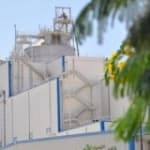
Octal, one of the largest PET producers and the largest PET sheet producer in the world has announced that phase two in the expansion plan of its state-of-the-art PET Complex in Salalah has been successfully completed within budget and on time.
Following the ramp-up period, full production is expected by August, fortifying the company’s ability to serve the North and South American markets’ dedicated capacity commitments. Phase two capacity takes total system output to 920,000 tons per year of PET bottle-grade resin.
Octal is totally committed to supporting wholesale conversion of large food and consumer product companies’ packaging requirements to PET and DPET sheet in North and South America. Octal has emerged to be a truly global supplier as a result of its dedicated capacity and supply chain capabilities for North and South America. The increased capacity will also support companies converting new packaging applications to DPET sheet for packaging of yogurt, meat, cheeses, and produce.
“Octal is building its brand on a truly global scale,” said Vivek Harkauli, Director, Octal’s Marketing PET Resin. “Our aim is to move into market leadership positions with multi-national giants such as Coca-Cola, Nestlé, Colgate and P&G. By growing our very profitable PET resin business, we have established a strong and stable base from which to drive targeted expansion into markets such as North and South America.
The unprecedented environmental advantages of Octal’s DPET sheet has also encouraged companies to use this proprietary packaging material. Compared to traditional plants, Octal’s DPET sheet uses 67% less grid electricity per kg of sheet, a fact that has been verified by independent, third party sources such as Intertek Expert Services, an internationally recognized, independent testing service.
“The Octal DPET process brings the major advantage of a carbon footprint 25 percent below that of traditionally produced APET films. The direct-to-sheet process eliminates the most energy-intensive and defect-prone processes to deliver a spotless sheet with a fraction of the energy,” stated William J. Barenberg, Jr., Octal’s COO. “Thermoformers have been able to reduce cost by ordering a thinner sheet, gain additional business by providing a clearer package and meet many new sustainability requirements from brands and end users.”
The next two years hold enormous promise for Octal which is now uniquely positioned to become the largest PET packaging company by delivering the benefits of technology and innovation. The company looks forward to continued growth with this new capacity dedicated to the North and South America market.