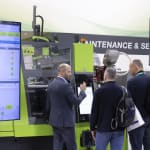
Exploit potential, tackle challenges, shape the future: how digitalisation and AI advance the plastics sector
K 2025, the world-leading trade fair of the plastics and rubber industry, has set out to tackle the central challenges of our time and present concrete solutions from 8 to 15 October in Düsseldorf. This aim is also reflected by its guiding topics. One of them reads “Embracing Digitalisation”.
The plastics industry faces major economic and regulatory disruptions worldwide. Rising competitive pressure, stricter environmental regulations and higher demands made on circularity increase the pressure to innovate. On-going digitalisation offers new opportunities for producing more efficiently and sustainably here. Automated processes, data-based control systems and smart connectivity already ease adaptation to stricter requirements in many companies today. The Federal Ministry for Economic Affairs and Climate Protection’s (BMWK) Digitalisation Index 2024 provides an indication of the increasing level of digitalisation and has found that the German economy has become around 14% more digital in the last five years. This has increased especially fast in the category “Processes” which describes both the digital maturity of intra-company workflows and the connection with external partners.
Artificial Intelligence (AI) is considered a key milestone in this. According to a Bitkom study, 78% of the industrial companies polled view AI as decisive for their competitiveness while more than half are waiting to see how others get on first. At the same time, 48% lack the necessary AI skills and 91% demand fewer regulatory obstacles so as not to hamper AI innovations. These figures underline that there is broad consensus on the relevance of digitalisation but many firms are hesitant to implement it in practice.
Digital key technologies: connectivity and IoT
The digital control and connectivity of machines forms the basis for new technologies. “In plastics machinery construction automation has already been ongoing for over 40 years. Now nearly all go one step further and bank on digitalisation,” says Ulrich Reifenhäuser, Chairman of the Advisory Board at K in Düsseldorf. Cyber-physical systems (CPS) and the Internet of Things (IoT) make it possible to capture and evaluate production data seamlessly in real time. Sensors monitor temperature, flow rate or in-mould pressures, for example, and transmit the values to Cloud applications. An important communication standard for this is OPC UA, which makes for safe and cross-manufacturer data exchange.
Rising data volumes lead to questions of data use. According to industrial associations, the so-called “EU Data Act” has created clarity on this now. The new Data Act obliges machinery manufacturers to provide machine users with the data generated during operation in a simple and understandable, machine-readable way. At the same time, predictive maintenance moves into focus because real-time analyses can detect deviations early on and reduce unplanned downtimes.
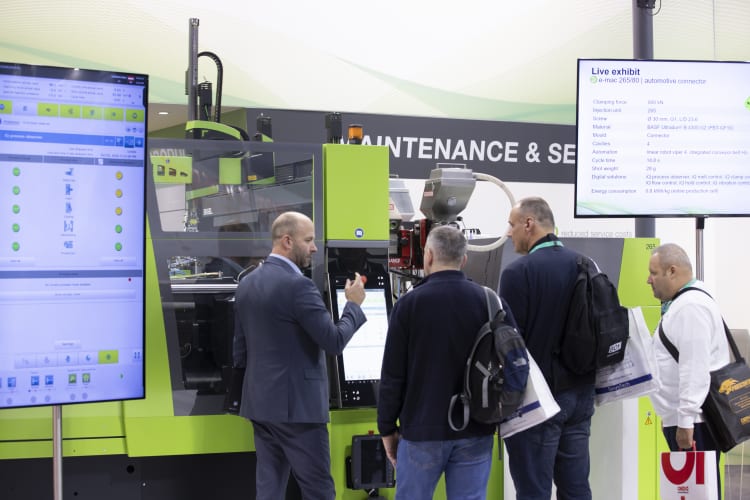
Artificial Intelligence and automation
AI adds new dynamism to digital processes as self-learning algorithms analyse large data volumes and optimise processes flexibly. “AI and digitalisation are game changers for the circular economy of plastics. Fully automated manufacturing processes, digital product passports and simulations make for optimised workflows and help save resources across the complete value chain,” says Dr. Alexander Kronimus, Deputy Managing Director at PlasticsEurope Deutschland, in an industry interview.
In addition, machine learning accelerates development cycles and improves process control. Digital twins go even one step further: they depict real production lines virtually and deliver structured data on the complete machinery utilisation. Furthermore, they offer the possibility to save machine data and information in a structured and machine-readable format over the complete lifecycle. Digital twins are said to also comply with the requirements of the Digital Product Passport (DPP), which was introduced with the EU’s Ecodesign for Sustainable Products Regulation (ESPR) entering into force in July 2024. These virtual twins of real manufacturing plants accelerate development cycles and ease maintenance strategies.