Optical quality control & AI-assisted sorting
In the field of quality assurance camera systems and AI-based image processing support manufacturing processes. They detect shape deviations, surface defects or material impurities during production and ensure consistent quality levels. These technologies allow early defect detection thereby reducing rejects and ensuring a more efficient use of resources.
In the wake of stricter environmental regulations and rising customer expectations the fitness of plastics for circularity is also moving centrestage. AI-assisted sorting systems with near-IR sensors (NIR) identify different plastic types, separate high-quality recyclates from impurities and improve the recycling quality. This increases reuse rates and contributes to compliance with regulatory requirements.
What’s more, digital systems are closely linked with the DPP, which features comprehensive information about the used raw materials, production processes and recycling paths. These technologies support companies in establishing closed material cycles, reducing environmental burdens and complying with the ESPR.
Challenges and skilled labour shortage
Despite numerous lighthouse projects progress is faltering in many companies, especially in SMEs. “Many small and medium-d enterprises have not sufficiently invested in digitalisation since this is associated with substantial costs and dependent on specific skills,” reports Mauritius Schmitz of the Institute for Plastics Processing (IKV) talking to the Industry Association for Plastics Packaging (IK). Another obstacle is the shortage of skilled staff. Those wanting to introduce automation, AI and IoT technologies require specialists for data analysis and IT security. This staff and skills shortage occasionally slows down implementation even though technical solutions already exist. AR (Augmented Reality) goggles can provide relief here by displaying maintenance instructions or training content right in the staff’s field of vision. This accelerates maintenance and onboarding processes without always having external experts on site.
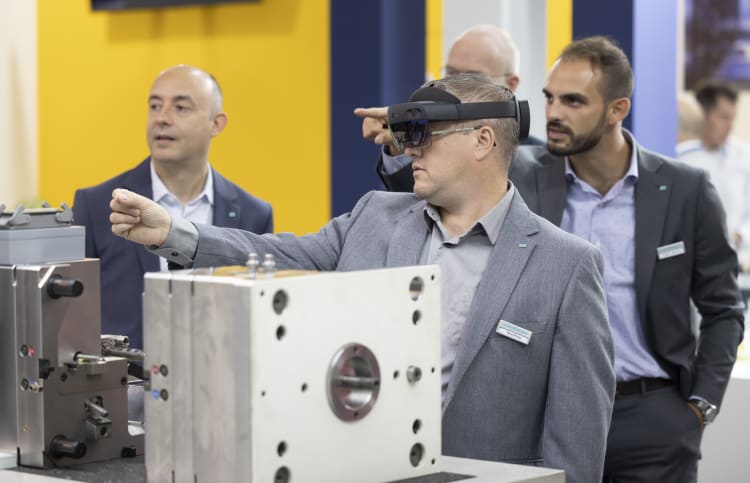
Summary & Outlook
Digitalisation proves to be a catalyst for a more sustainable and efficient plastics industry. Connected production systems make for real-time optimisation thereby reducing rejects rates and buffering market fluctuations more confidently. At the same time, new business models can be developed - in the form of digital platforms and maintenance services, for example. A crucial role, however, will be played by funding. According to the Leibniz Centre for European Economic Research (ZEW) the plastics industry invests EUR 2.2 billion in innovation, a sum that only corresponds to 1.65% of the innovation expenditure of the processing industry as a whole. At the same time, the ZEW points out that 63% of companies in the sector are active in product or process innovations, which exceeds the average of 57% in the processing trade. These figures illustrate that there is a will to innovate but financial and human resources are needed to consistently implement digitalisation projects.
At K 2025 the enormous potential that digitalisation holds for the plastics sector will be both highlighted at the over 3,000 exhibitor stands and flagged up at the various Specials that also address the challenges - first and foremost the official K Special “Plastics Shape the Future”, organised by Plastics Europe Deutschland, or also the VDMA Forum.