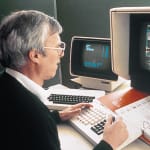
Nowadays, digitalisation plays a key role in tool and mouldmaking. Hasco, as a leading supplier of modular standard mould units and accessories, has become a pioneer in the digitalisation of an entire industry through the constant development of unique standards. The opportunities provided by digitalisation in the company were recognised at an early stage, and Hasco implemented them back at the beginning of the 1980s to make the design and production of mould systems as easy as possible.
Hasco was offering support with design at a time when nobody was yet thinking of Computer Aided Design (CAD). A "blueprint book" was a welcome aid on the drawing board. Also at that time, the manual with Hasco design examples would never have been missing from a mould designer’s shelf. The first steps along the digital road were made within the company in the moulding technology and machine engineering department, when data coupling with machines, production data acquisition and product traceability were introduced.
This was followed in 1982 by the procurement of the first CAD system from Unigraphics and the introduction of the Hasco standard mould unit module, which enabled designers and mouldmakers to configure complete mould systems with the respective accessories directly from the system provided. This was an important milestone, because Hasco was the first on the market to make this digital service available to its customers in the form of a standard mould unit library. From the drawing board to the digital workplace - the digital workplace and also computer-aided working were equal to a paradigm change in the industry. After the invention of the modular system for standard mould units in the 1960s, Hasco fundamentally changed once again the thinking and acting of an entire industry several decades later.
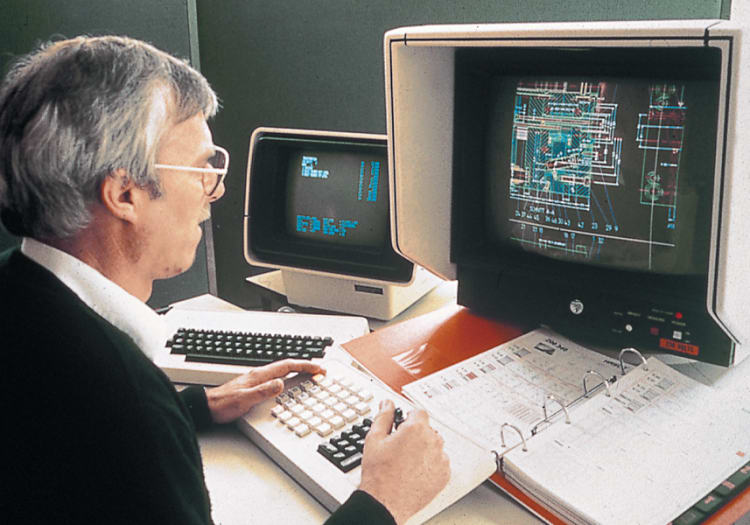
The basic concept of the standard mould unit module was, from then on, continuously extended and optimised. In 1997, the first version then appeared in 3D with three-dimensional data, which today still form the basis for the design of moulding tools. One year later, the digital system was extended with an online ordering service. Via the homepage, which at that time received an award as the most modern website, it was possible to order all plate and accessory components comfortably and easily on the own computer. At the same time, this simplified the price calculation of a mould system.
It is nowadays impossible to imagine day-to-day business without digitality. Internally, manual production and service processes gradually had to give way to digital systems. This increased delivery capability and substantially simplified the manufacture of Hasco’s quality products. Stocks and logistics were digitalised to speed up delivery processes even further and give the customer greater flexibility. The products, too, have long since arrived in the digital age. Certain articles are now, for example, supplied with an OPC UA interface. With the help of the recently released Mould Track, precise indoor localisation of injection moulding tools is now possible.
Hasco hot runner is treading further innovative paths here, bringing RFID technology to hot runner systems.
As a pioneer of digitalisation, Hasco has repeatedly simplified work processes and, with more innovations for the future, is once again setting standards in terms of efficiency and productivity.