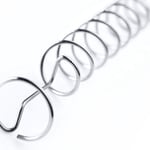
Innovative Cooling Tornado Z9665/… - Saving energy directly in the mould
With the new Hasco Cooling Tornado, Hasco is providing an innovative solution for increasing efficiency and saving energy during the cooling of the mould.
The Cooling Tornado Z9665/... offers a variety of application possibilities and can be used both in combination with runners in core cooling systems and directly in the corresponding cooling bores. Through the production of a turbulent flow, the effectiveness of the cooling is increased by up to 20 % (depending on the flow l/min). This turbulence interrupts the laminar lower layer of the cooling medium and has the effect that also the inner core of the cooling medium flows to the outer sheath, and thus considerably improves the heat transfer.
Turbulent flow for efficient cooling
The Cooling Tornado allows, through the turbulent flow, efficient cooling for shorter cycle times and the avoidance of hot spots, which ensures uniform temperature distribution. Compared with conventional cooling bores, temperature differences of up to 10 °C can be attained. The turbulence of the cooling medium leads to an energy saving of between 20 and 40 %. The Cooling Tornado allows easy retrofitting as well as the possibility of customised shortening, making for uncomplicated installation on existing systems.
The installation itself is also extremely simple. The Cooling Tornado can be quickly retrofitted and is simply positioned and fixed at the end via a clamping ring. The mounting can both be carried out in combination with cooling pipes such as Z962/... for core cooling and also directly mounted in the cooling bores.
Energy saving directly in the mould
Extensive tests confirm the effectiveness of the Cooling Tornado Z9665/.... In a comparison of the cooling circuits with and without the use of the Cooling Tornado, a reduction in the surface temperature of 10 % was measured. With a flow rate of, for example, 6 l/min, the surface temperature of the cavity fell from 86 °C to 78 °C. These results show that, by fitting the complete mould with the Cooling Tornado Z9665/..., an energy saving of 20-40 % can be achieved.
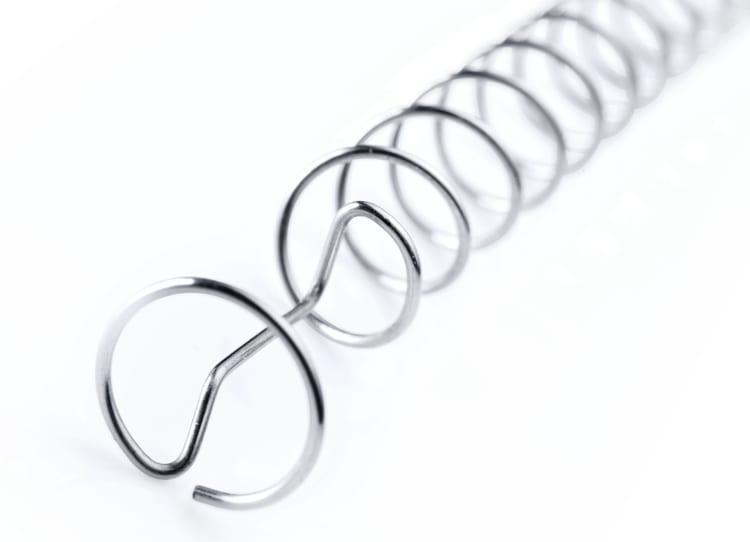
Innovative Shadowfree technology as module element eliminates shadow formations in valve gate systems
In conventional injection moulding, undesirable, poorly flowing areas often occur in the hot runner due to roughness around the valve pin. This results in degradation reactions in the plastic melt and exceptionally long colour transitions.
The innovative Shadowfree technology as module element eliminates the flow shadows in valve gate systems and enables a significantly faster colour change in the hot runner.
Uniform flushing around the needle
The 3D-printed, floating system effectively splits the material flow into streamlined channels to evenly flush around the needle and reunites them at the point where the valve pin enters the melt channel. Rigorous testing has shown that the system provides a rapid transition from black to white material in just 25 cycles, outperforming conventional valve gate systems by three to four times.
In addition to the proven advantages of the Streamrunner, such as the elimination of dead spots, a particularly gentle material flow and thus a noticeable reduction in pressure losses, the Shadowfree technology now also offers a solution for extremely sensitive materials in terms of heat stability in combination with valve gate systems.
With the additively manufactured Streamrunner, Hasco started a new era in the world of hot runner technology. It was developed with state-of-the-art technologies for innovative future-oriented solutions. The compact and perfectly balanced Streamrunner ensures particularly gentle melt guidance in combination with excellent colour change characteristics. The leak-proof system is also particularly suitable for multi-cavity systems.
Super-fast colour changes with valve gate systems
The Streamrunner Shadowfree is now well on its way to further revolutionising the manufacturing landscape. With up to 70% faster colour changes, the system enables material losses to be reduced and product quality to be increased.
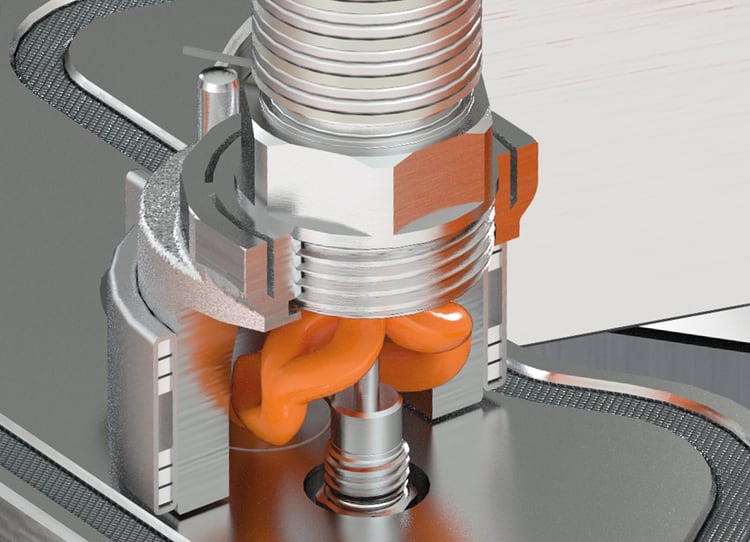