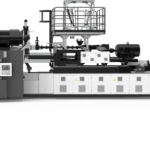
We, the BOLE Intelligent Machinery are sure that plastics will not disappear from our everyday life. Our task, however, is to consider how to handle this valuable material in a way that conserves resources.
Therefore, BOLE Intelligent Machinery, together with a young and innovative company in Germany, has launched a program (www.tomorrowthings.com) to really reduce the consumption of plastics at the processor of plastics over the complete process. In addition to the pure production process, all secondary processes are also considered and analyzed, and then the operators of the machines are informed and guided in a targeted manner about what needs to be done on the equipment in order to consume less material.
Recycling, the solution ?
Another approach is of course the recycling of plastics. Here, BOLE Intelligent Machinery has been using machines for quite some time, since especially in BOLE's home market the recycling of plastics has been a very high priority for several years due to the costs of the basic materials. This machine consists of a basic injection molding machine with a single or twin screw plasticizing unit, a filtration system and a screw injection unit.
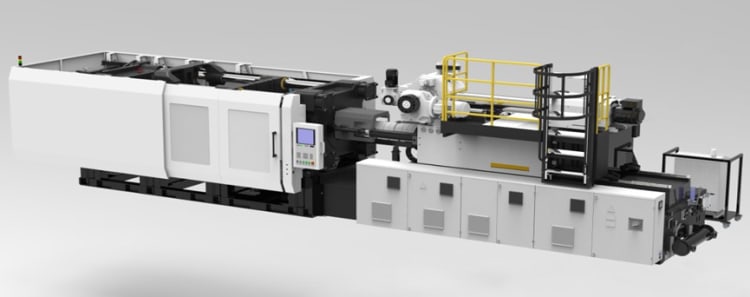
With this machine, recyclates are produced very cost-efficiently without complex upstream recycling processes to plastic components with characteristic of parts from virgin material.
The standard plastic ?
For closed-loop systems, we must achieve standardization of the basic plastics in the future. However, we will not be able to cover the required range of technical properties with standardized plastics. We, BOLE Intelligent Machinery, therefore believe that more and more processors will be given the task of refining these standardized plastics. For this purpose, BOLE has direct compounding injection molding machines in its product range.
In these machines, a wide variety of additives and fillers such as talc, glass fiber, etc. can be added to the standard plastic via several material feeders, thus changing the property directly at the machine.
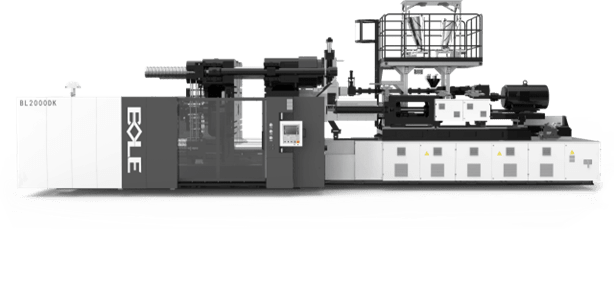
If you also look at the CO2 balance, you can see that a significant reduction is possible. Since the unit plastic is melted only once. The unit plastic and the additives are not sent to a compounder and from there to the processor, which results in a significant reduction in transport costs and emissions.
Two - and multi-component part of the solution ?
Our well-known technologies, such as in this case two-component injection molding, should also not be lost sight of. Since with the use of unit plastics, combinations between a plastic and a modified plastic on the same base will certainly come more and more on the market. For example, a material unreinforced for a surface combined with a reinforced material on the same plastic base for strength for the part. For these applications, machine technology will be needed in the future, which must be very flexible to use and approach the price level of a standard machine.
Here, BOLE relies on its special technology of moving the units horizontally and vertically in relation to the fixed machine platen, so that the customer can define an optimum gating point depending on the mold and component and thus significantly reduce costs in the hot runner area.
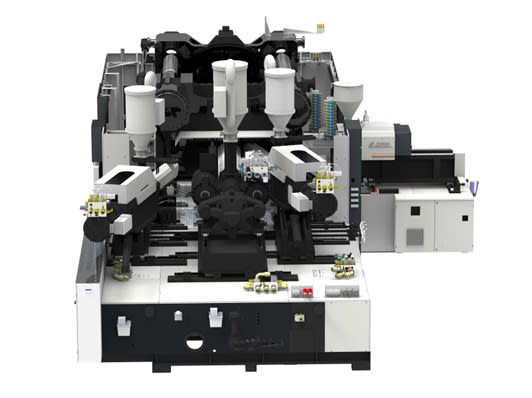
Furthermore, we must also develop solutions in the future to easily adapt the existing machinery for the new process technologies, BOLE can also support you with our conversion and retrofit program for our and your existing machines.
Freely according to the motto, the best CO2 balance reduction is to use the existing machines and adapt them accordingly to the new world.
Bioplastics, Polyman what do you say?
Bioplastics are on everyone's lips now, but most of the talk is about the classic replacement of plastics in packaging. It should be known that the range of bioplastics is much wider at present.
It is of course possible to obtain bioplastics with MFI of more than 100 for the production of thin-walled packaging on the market, which decompose after a certain time under certain conditions.
However, it is also interesting to note that there are bioplastics that have the same technical properties of engineering plastics and are just as durable.
What's exciting is that at the end of the product's life cycle, these bioplastics can be recycled or fed into a composter and allowed to decompose while releasing energy.
As this topic is very exciting for BOLE, BOLE has agreed to cooperate with Exipnos in the field of bioplastics.
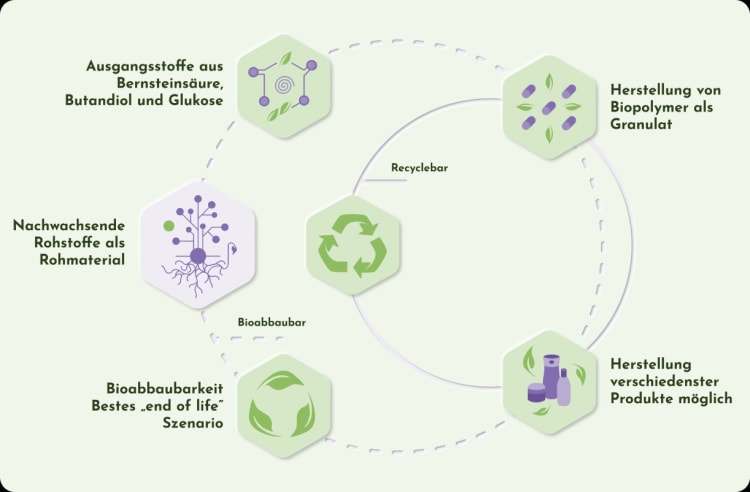
The background is that BOLE is of the clear opinion that machine technology will change with the use of biopolymers and that adaptations to machine technology in the area of plasticizing, heating and drive technology of injection molding machines will be necessary for the economical production of components made of bioplastics with the lowest energy balances.
Here, BOLE Intelligent Machinery will want to take a leading position, as it is already doing in China. Therefore, we are looking forward to an exciting collaboration with the Exipnos team.
Timo Günzel (Dipl.-Ing.)
CTO (Chief Technology Officer)
Bole Intelligent Machinery