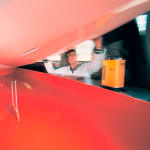
Rotor blades have to withstand extreme stresses. Their quality depends not least on the reliability of their adhesive bonds. Germanischer Lloyd has certified the first polyurethane adhesive for the wind power sector: Henkel’s Macroplast UK 1340. The new technology offers multiple benefits when compared to epoxy systems, allowing wind turbine manufacturers to optimize productivity, improve quality and reduce costs.
Frekote mould release agents, backed by over 40 years of research and development, are the global industry standard for performance, quality and value. A comprehensive range of Frekote release agents is formulated to provide the maximum number of releases for composite systems including Epoxies, Polyester, Vinyl Ester and Polyurethane.
Whilst epoxy chemistry has been a great servant to various industries for decades, the engineers at Henkel are always searching for new methods to improve the structural assembly process.
The goals of Epsilon resins are to enhance mechanical performance and durability, while lowering some of the costs associated with composite structure during manufacture and service. In addition to such high performance attributes as low cure shrinkage, low water absorption and improved thermal stability, Epsilon resins also meet the customer demand for process ease, lower weight, and cost savings.