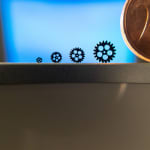
Some 30 years ago now, additive manufacturing (AM) - which back in the day was more typically known as rapid prototyping, - disrupted (as the name suggests) the prototyping stage of product development. The ability to print parts in 3 dimensions from CAD solid models facilitated concurrent engineering, as within days of a design being complete, all relevant product development departments could sit together analysing an accurate prototype, and designs could be easily re-iterated to overcome potential downstream manufacturing issues. For a tooling manager to be able to initiate changes in product designs to streamline the tooling process a few days into the development of a product knocked weeks if not months off product development cycles.
Move on 25 years, and AM began disrupting the traditional manufacturing paradigm once again, this time in the area of production. In general terms, AM technologies have become increasingly sophisticated over time, and the precision and accuracy of builds in a variety of materials means that AM is now challenging legacy manufacturing processes in terms of speed, cost, and tolerance attainment.
This history of AM over the last 30 years, however, is only really accurate when looking at the production of macro-d parts and components. It is only in the last few years that AM has been able to disrupt the area of micro manufacturing, as it is only in the last few years that innovators have managed to refine the AM process to achieve the micron level tolerances and surface features that have been the preserve of legacy production processes such as micro molding for decades.
Today, however, micro AM processes like the Fabrica 2.0 from Nano Dimension that we use at Accumold can now additively build parts and components only previously possible through the use of micro molding, and can do so in a way that allows manufacturers to completely re-imagine the way that precision micro parts and components are made, and which changes the basic economics of manufacturing.
The Fabrica 2.0 can attain 1.9 micron resolution in X and Y, and the technology builds “additively” in 1-5 micron layers. With this breakthrough, the path to the creation of innovative miniaturized parts at amazing speed and reduced cost is open for all industry sectors.
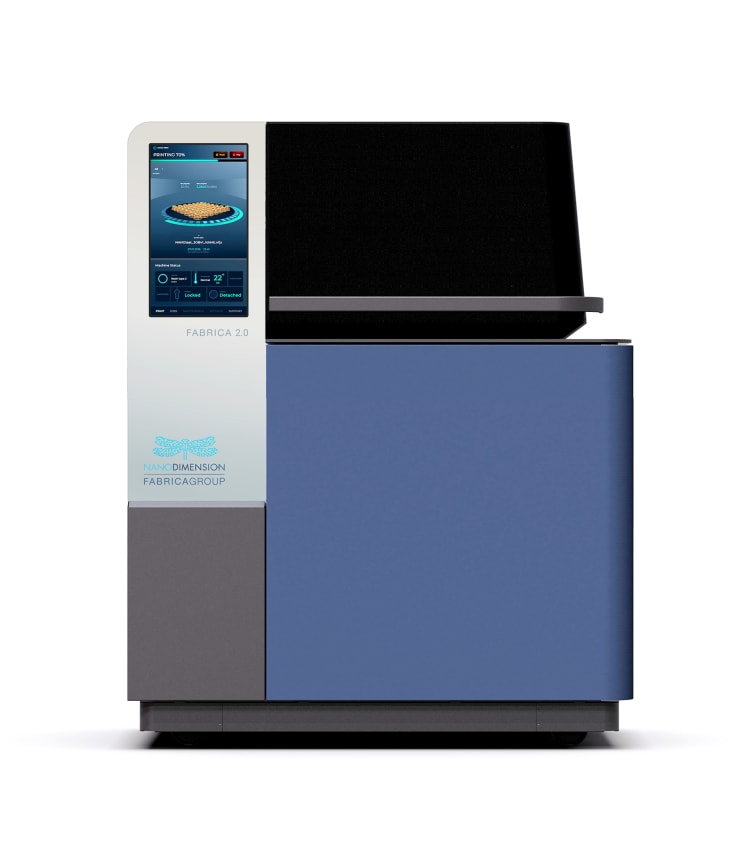
The Nano Dimension Fabrica 2.0 machine
What does this mean for manufacturers
The Fabrica 2.0 micro AM platform promotes innovation, and stimulates cost and time-to-market reductions. But in general terms, success through the use of the Fabrica 2.0 is measured in microns and hours. Micron-level detail can be achieved without the need to fabricate tools, and this means that you can have intricate and geometrically complex prototypes in a matter of hours.
There is a limit to the ability to create complicated parts using traditional micro tooling. With increased complexity comes increased cost, but not when using the Fabrica 2.0 micro AM technology. The absence of the requirement for a physical tool lifts the lid for design engineers to think out of the box and attain design goals previously unimaginable. This design freedom coupled with the inherent manufacturing agility that is a core characteristic of AM require a root and branch re-assessment of all aspects of the product development process, a disruption that is a spur to the stimulation of future product successes and enhanced market-share and profitability.
Through the use of the Fabrica 2.0, you can also optimize workflow, the technology producing less scrap and fewer tools than conventional manufacturing processes. It also promotes the reduction of iterative process, assembly, and inventory. This means that significant operational cost benefits are now attainable at the micro manufacturing level.
But there’s more! Through a combination of design optimisation and improvements in materials, we are able to additively manufacture Direct Rapid Soft Tooling (DRST) which we can use to injection mold real parts. This unlocks new business possibilities for mold makers and manufacturers who up until this point have been restricted to the use of long lead time and expensive traditionally manufactured mold tools for the achievement of any volume of molding, from prototype runs all the way through to mass manufacture. The business case for a process chain that includes DRST, with dramatically shorter lead times at reduced cost is obviously compelling.