Case Study 2 - Implant Tip
Another one of our medical device customers needed to finalize an implant tip design measuring 1.5 x 3.0 x 2.5 mm before the design freeze date. The customer needed a frozen design so that they could kick off tooling and not push out their overall project timeline. Using the Fabrica 2.0 we were able to print 16 different tip designs for the customer to evaluate. Again, we could print a lot of parts in the Fabrica 2.0 print envelope, and our first print included 10 samples of each of the 16 design iterations. It took less than 24 hours to design, print, post process, package, and ship the parts to the customer, which completed its testing in a few weeks and came back with 6 different modified designs for another round of testing. Our second print was turned around in about one day so the customer could quickly resume testing.
Once all testing was completed, the customer shared with us their frozen design. With that, we kicked off our mold manufacturing process with a DFM session to ensure the molded thermoplastic part would meet the quality and functional requirements defined by the customer. With project work starting a couple months prior, we already had an established line of communication with the customer so we could quickly design the production tool and production process understanding all the criteria that needed to be met.
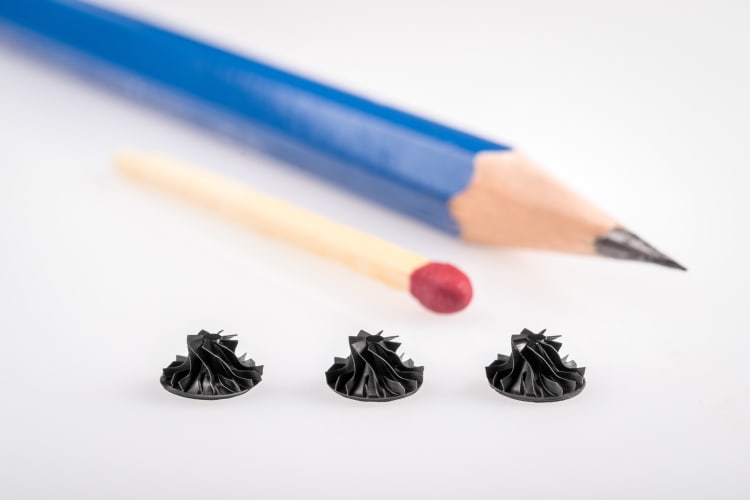
Impellers made using the Nano-Dimension Fabrica 2.0 micro AM machine. The impellers are used to increase pressure and flow rate of a fluid, and measures x 5.66 mm, Y 5.66 mm and Z 2.87 mm
Case Study 3 – Valve Assembly
The last example comes from another medical customer that was trying to finalize the design of a valve assembly measuring 9.0 x 9.0 x 10.7 mm. This valve was comprised of a softer material overmolded on top of a harder machined part. The valve needed to maintain a seal while being rotated within the final assembly.
Our first round of samples was molded in DRST with the Versaflex material. Testing found that we had a few dimensions out so the insert CAD models were updated, and new inserts printed a day later. The second round of samples worked better but we found the Versaflex was too rigid when rotating it in the test assembly. We then used the same printed inserts to mold parts in Sarlink. The Sarlink parts performed better in the test assembly, but some leakage was observed. Sources of the leak were identified, the CAD models were modified, and another set of inserts were printed. This final set of inserts produced valves that could be easily rotated in the assembly and did not leak.
From start to finish we were able to test three different DRST mold designs and two materials in about two weeks. The customer was extremely pleased with the results and was excited by how much we learned in such a short period of time.
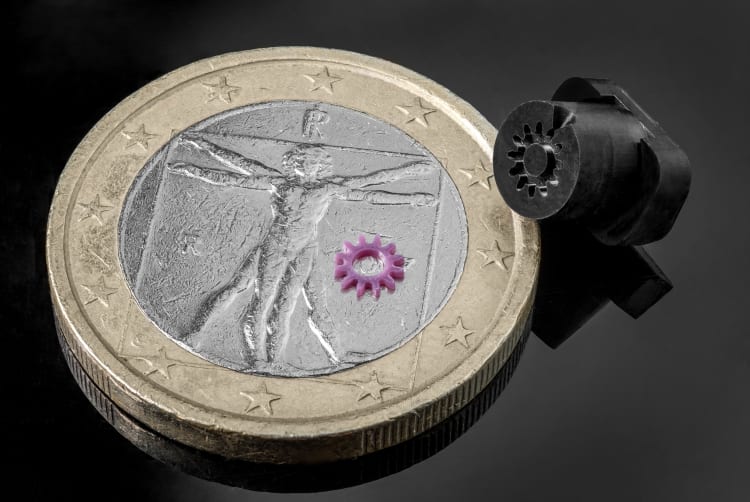
A direct rapid soft tool made on the Fabrica 2.0 micro AM platform
Summary
All of the successful case studies discussed would not have happened without the Fabrica 2.0 micro AM technology being used as a central tool in the product development process. Fundamental to the success of the Fabrica 2.0 is that it brings the benefits of AM to micro manufacturers for the first time, including hitherto impossible part complexity (enhancing design and functionality), no tooling costs, minimal set up costs, the ability to mass customise and personalise products, and the ability to produce DRST. As a versatile technology appropriate for prototyping, small batches, and potentially even mass manufacturing, the technology is now stimulating innovation in the micro manufacturing sector, and is truly changing the economics of manufacturing.
Christopher Hunt, Additive Manufacturing Manager, Accumold