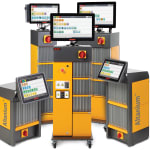
Husky Technologies, a pioneering technology provider enabling the delivery of essential needs to the global community, today announced the launch of a second-generation control algorithm for its line of Altanium mold controllers. The Advanced Reasoning Technology (ART 2.0) software delivers greater speed, accuracy, precision, and repeatability compared to today’s existing temperature control systems.
ART 2.0 incorporates advanced auto-tuning and heat-up strategies which deliver higher out-of-the-box performance. It consistently delivers high accuracy and control precision, significantly reducing variability in the molding process shot-after-shot and mold-after-mold. Test results show that ART 2.0 delivers up to 42% faster heat-up times with 30% less energy use.
“We’ve elevated our controller technology to a new level,” said Aurelien Bastien, Husky’s President of Hot Runners, Controllers & Medical. “The all-new tuning and control solution enhances performance while increasing productivity and significantly impacting a molder’s bottom line.”
ART 2.0 includes two complementary heating solutions, which upgrade Husky’s original ART Classic control solution. The primary heating strategy is UniStart which offers uniform and homogeneous heating while promoting even thermal expansion of components in the hot runner. UniStart distinguishes itself by finding the right balance between applying full power to the slowest heating zone and controlling overshoot to minimize heat-up and stabilization time.
A complement to UniStart is AltaStart, a patent pending advanced algorithm which staggers heating so that all zones reach process temperature simultaneously. Power is not applied to lower mass zones until the last possible moment, reducing material residence time and minimizing degradation in areas like the nozzles with less melt volume. AltaStart also reduces energy consumption by bringing the fastest responding zones, such as the tips, to temperature last.
ART 2.0 also provides auto-tuning capabilities that ensure a high level of control with minimal to no user interaction. Unlike competitive systems with limited tuning outcomes, the ART 2.0 system has more available tuning choices to deliver high level control. It uses individually adjustable P, I, and D values for selection during the auto-tuning routine, increasing the chances of arriving at an optimal result by limiting any gaps that a zone may fall into using the one-parameter method.
Based on benchmark testing, ART 2.0 also provides a significant return on investment (ROI) due to the system’s ability to reach set point and stabilize the process faster. “Based on the benchmark testing, we start making good parts sooner than conventional control systems,” said Bastien. “We achieve a faster payback because we produce more parts in a shorter period of time.”
The Altanium mold controller, powered by ART 2.0, has proven to be the most user-friendly based on a standard setup procedure for qualifying new molds. An expert operator achieved a 64% increase in productivity based on understanding the steps to execute adjustments and the number of button presses to complete the steps versus competitive technologies. A highly functional human-machine interface (HMI) delivers this enhanced usability, reducing complexity and minimizing button presses.
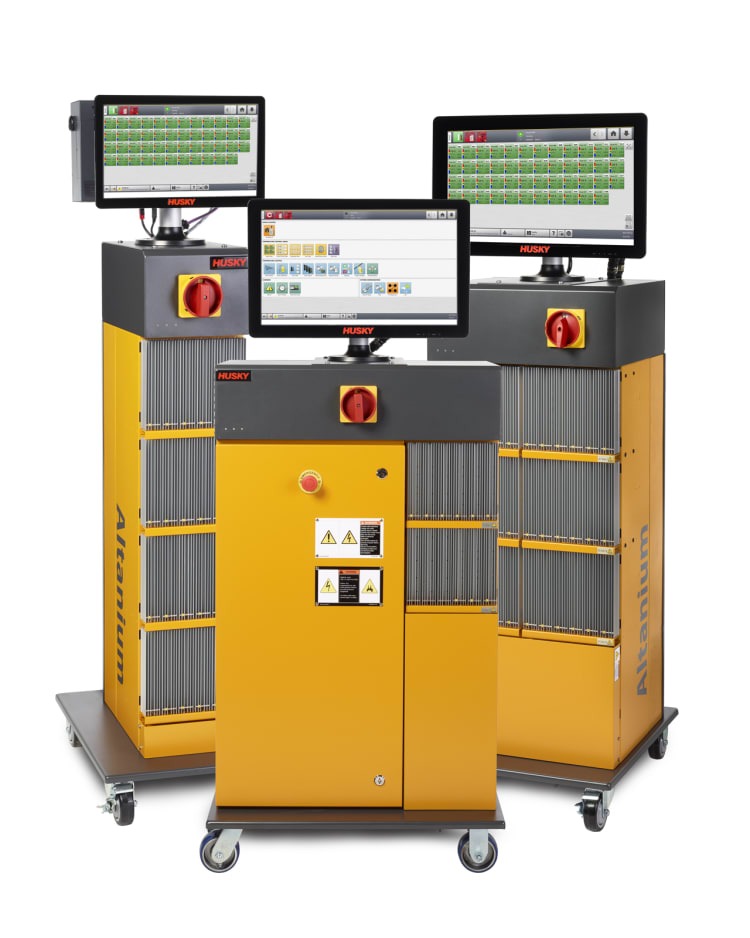