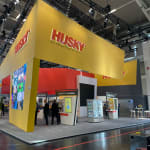
Husky Technologies, a pioneering technology provider enabling the delivery of essential needs to the global community, has returned to exhibit at Drinktec 2022 in Munich, Germany from September 12-16. Husky’s booth (Hall C4, #425) is showcasing the company’s latest technologies, solutions and services engineered to enable liquid food and beverage producers to achieve growth, sustainability, flexibility, differentiation, and world-class production capabilities.
“As markets around the world continue to evolve, beverage producers are being challenged to adapt to new realities that range from rising energy and material costs, to supply chain fluctuations, to skilled labor shortages, to demands to be more sustainable, to name a few. All of which can create variability and uncertainty in their operations now and into the future,” said Robert Domodossola, Husky’s President of Rigid Packaging. “We are excited to be back exhibiting at Drinktec 2022 to highlight how our complete portfolio of technologies, solutions and services work together to help beverage packaging producers around the world respond to these challenges with certainty.”
Enabled by Husky. Powered by People.
At the show, Husky is showcasing its versatile range of solutions that:- Enable Growth by streamlining the adoption of world-class manufacturing processes that facilitate speed to market through automation and digitization.
- Enable Sustainability by developing technologies to produce high quality packaging that supports the circular economy, is lighter weight and contains more rPET material
- Enable Flexibility by implementing manufacturing solutions designed to help producers quickly adapt to continuously changing consumer demands and market trends
- Enable Differentiation by developing tools to produce attractive, safe and sustainable PET packaging that out-performs alternative materials and stands-out on store shelves
- Enable Stability by offering reliable, energy efficient manufacturing solutions that reduce variability, as well as boost material and operational efficiency
Introducing HyPET Complete
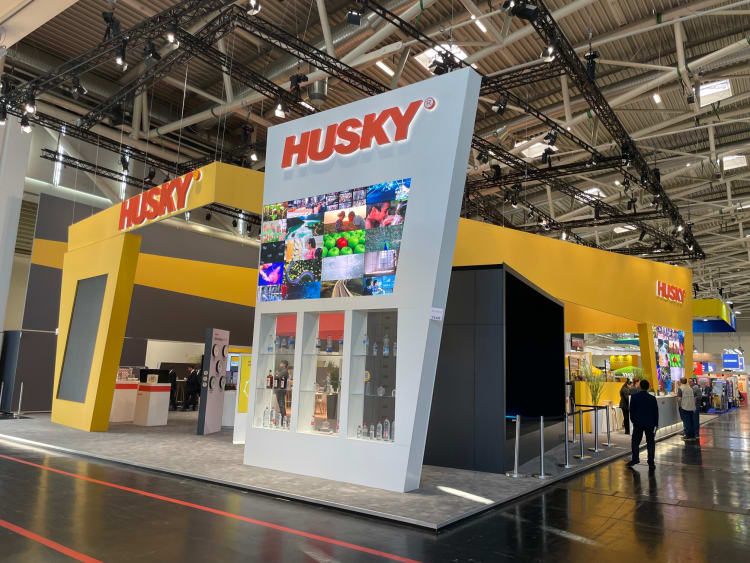
At the show, Husky is also introducing HyPET Complete - the industry’s only complete, end-to-end, connected production solution. Developed to address ongoing top-of-mind challenges of global producers, HyPET Complete is modelled to transform variability into stability throughout every stage of PET preform production.
“To truly succeed in today’s global climate, it has become clear that to be competitive producers need to think beyond just hardware to a more holistic approach to manufacturing,” said Domodossola. “HyPET Complete goes one step further enabling producers to build more
resilient, stable manufacturing models that are less affected by shifting external factors. This is particularly relevant today as we see producers who are increasingly looking for more energy efficient manufacturing processes and packaging materials, such as PET, to offset fluctuating
costs.”
HyPET Complete was founded on a holistic approach that incorporates factory planning and tooling lifecycle optimization, workforce training and development, a fully digitized delivery model and OEM parts solution, as well as the company’s recently introduced Advantage+EliteTM proactive, predictive and transparent monitoring solution. All components are designed to work together to enable producers to successfully navigate through today’s most prevalent challenges, including achieving circularity and sustainability, mitigating supply chain risks, preparing for skilled labor shortages, optimizing material and operational efficiency, as well as offsetting rising material costs and inflation.
Dedicated to continuous innovation, HyPET Complet is supported by Husky’s latest generation platform of proven HyPETTM systems tailored for the production of rPET that include a purpose-built drying solution, optimized energy management, enhanced melt control, automated mold cleaning, integrated part quality inspection, and more.