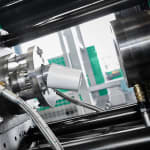
At Fakuma 2021, Arburg will be showing application examples of the sustainable production of mass-produced products as part of the "arburgGREENworld" focus. These include innovative solutions for recycling used products and the new recyclate package for Allrounder injection moulding machines. On show will be the injection moulding of products that can be sorted using marking technology (“HolyGrail” and “CurveCode”), and the processing of bio-based and recycled materials. Trade visitors can also get advice on all issues relating to sustainability and the conservation of resources.
As part of the “arburgGREENworld” programme, Arburg is intensively involved in the issues of resource conservation and the circular economy. The trade public at Fakuma can see for themselves the potential offered by sustainable plastic parts production using new “green” applications.
“CurveCode”: Recycled PP cups that can be sorted by type
The “Espresso Cup” application is an application example of how innovative products made from plastic can be manufactured sustainably and efficiently and returned to the cycle after use, sorted by type, with the help of a material-specific “CurveCode”. A hydraulic Allrounder 270 S with 350 kN clamping force produces a cup weighing around 20 grams in a cycle time of around 15 seconds. The original material is chemically recycled PP granules. This means that instead of using crude oil, the chemical raw materials are extracted from plastic waste and then processed further to form PP with the same properties as a virgin material.
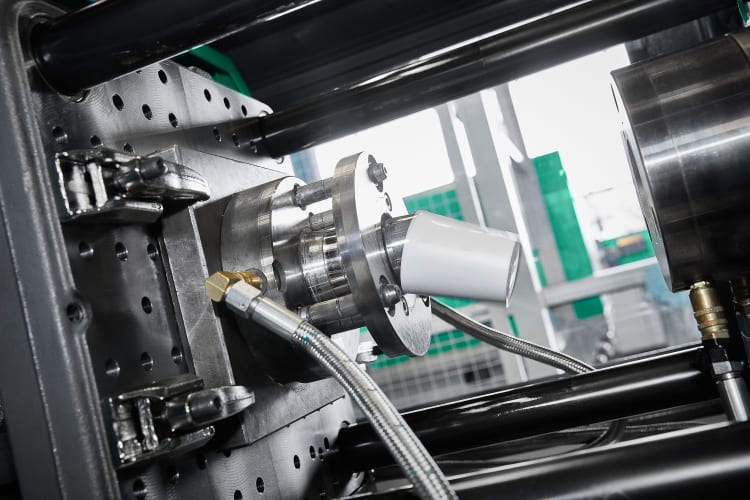
For separation by type: A “CurveCode” engraved in the mould is transferred to the injection moulded product almost invisible. In recycling plants, a camera system is able to read the information it contains.
A “CurveCode” from Filigrade is engraved in the single cavity tool. This engraving can also be added to existing moulds. In this way, a corresponding curve-shaped watermark that is virtually invisible to the end consumer can be applied to the product during the injection moulding process. In recycling plants, the waste products with “CurveCodes” can be read by a camera system by means of light reflection and selected as a "food-safe PP" material, for example.
HolyGrail: “Intelligent” sorting using watermarks
Another watermark technology for intelligent sorting is the so-called “HolyGrail”, which Arburg is presenting using the example of a sophisticated packaging application. The exhibit is a hybrid Allrounder 1020 H in the packaging version with 6,000 kN clamping force, a 7000 injection unit and Gestica control. With a 4+4 stack mould, the high-performance machine produces four thin-walled IML cups complete with lid in a cycle time of around five seconds each. These are then automatically deposited and stacked on a conveyor belt. The part weight is 19.3 grams. Both the cups themselves and the associated label and lid are made of chemically recycled PP. A mono-material product of this kind can be recycled economically and to a high quality after use.
This is exactly where “HolyGrail” comes in: The digital watermarks are postage stamp-d codes invisible to the end consumer - in this case, directly on the label. The individual tile patterns form a “digital passport”, a fragment of which is sufficient to retrieve information about the manufacturer, the materials used for disposal and whether it is “food-safe or not”, for example, using the appropriate app. The information can be read out in sorting plants with a high-resolution camera.
Turnkey system: Bio-based sunglasses, “ready to wear”!
A real eye-catcher are the “green” Uvex sunglasses made of transparent bio-based PA12 “Grilamid TR XE 4205 green” by Ems. This bio-plastic consists of 39 percent renewable raw materials based on castor oil, obtained from seeds of the castor bean. The bio-based sunglasses are produced on a “smart” turnkey system based on an electric Allrounder 570 A in a cycle time of around 50 seconds. The filling assistant is integrated into the associated Gestica control system, i.e. the machine “knows” the moulded part that it is to produce. Using automation, interlinking, and human-robot cooperation, a “ready to wear” product can be created efficiently, reliably and traceably in a single step. Pick-up and feed for optical inspection, laser marking and packaging is handled by a six-axis robot. In addition, the production cell is equipped with the Arburg Turnkey Control Module (ATCM) SCADA system, which enables 100% traceability of the parts.
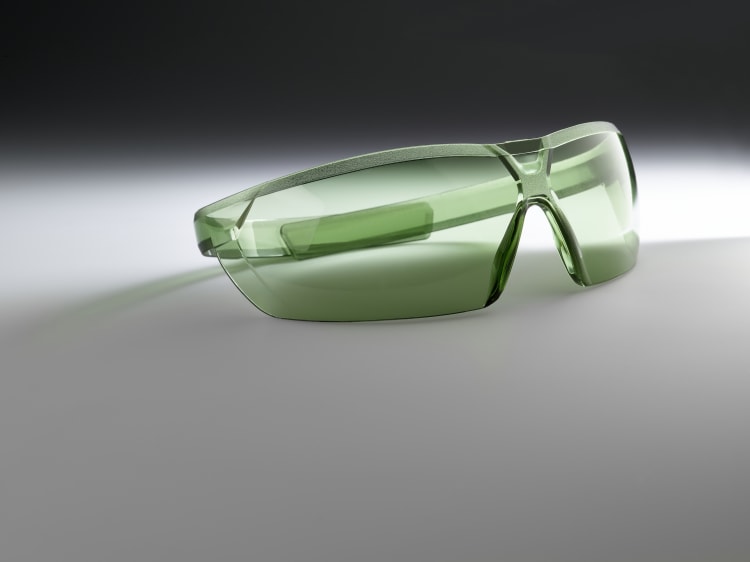
At Fakuma 2021, a turnkey system based on an electric Allrounder 570A will be producing “green” Uvex sunglasses from bio-based PA12.
New recyclate package
At the “Circular Economy” station, Arburg experts will be on hand to answer detailed questions on the topics of sustainability and resource conservation. A new recyclate package for Allrounders will also be presented there: A range of different controller functions and special equipment for plasticising ensure that recyclates can be processed safely.