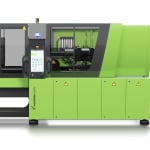
With its many years of injection moulding experience and outstanding automation expertise, Engel develops highly cost-effective production concepts for the manufacture of composite parts in large quantities. At JEC World 2023 from 25 to 27 April in Paris, the machine manufacturer - headquartered in Austria - is demonstrating how high production efficiency and cost effectiveness can be combined with sustainability for both the aerospace and automotive industries.
In the Engel organomelt process, thermoplastic fibre composite preforms - for example, thermoplastic sheet and UD-tapes - are formed and functionalised in a single integrated step. For example, reinforcing ribs or assembly elements are moulded immediately in the same mould after thermoforming using a thermoplastic from the same matrix material group as the thermoplastic sheet. This not only enables a highly efficient and fully automated production process, but also contributes to the circular economy. The consistent thermoplastic mono-material approach facilitates subsequent recycling of the parts.
At its stand in Paris, Engel is demonstrating the huge potential of organomelt lightweight technology with a live machine exhibit. An Engel victory 660/160 injection moulding machine and an Engel easix articulated robot are being used to automate the production of inspection flaps for the fuselage of passenger aircraft. The production cell also includes an IR oven, which also comes from Engel in-house development and production.
To showcase the wide range of applications in both the aerospace and automotive sectors, two different material systems are being processed alternately during the three days of the fair. On the one hand, thermoplastic sheets with a PEEK matrix are being overmoulded with a PEEK, while, on the other, PPA-based thermoplastic sheets are being processed in combination with PPA.
The thermoplastic sheets are heated in the IR oven, taken into the mould by the robot, formed in the mould and immediately overmoulded. The reinforcement ribs and a mounting clip are formed.
Heating up the thermoplastic sheet is a process step which determines the cycle time and is also relevant to quality. The thickness of the preform defines the heat-up and cool-down times. Heating up the material quickly without damaging it is important, as are short paths for transporting the heated thermoplastic sheet to the mould, to avoid the sheet cooling down again on the way to the mould and losing its malleability. This is where tie-bar-less technology of the victory machine plays to its strengths. Barrier-free access to the mould area makes it possible to position the IR oven very close to the mould. And the robot can take the shortest path to the mould without working around interference contours. Both factors accelerate hot handling and ensure process consistency and high component quality.
In integrated Engel system solutions, the robot and the IR oven are integrated into the injection moulding machine's CC300 control unit. This allows the entire process to be operated centrally using the machine display. Another advantage is that the injection moulding machine, robot and IR oven access the same database and precisely coordinate their motion sequences with one another. This reduces the cycle time in many applications.
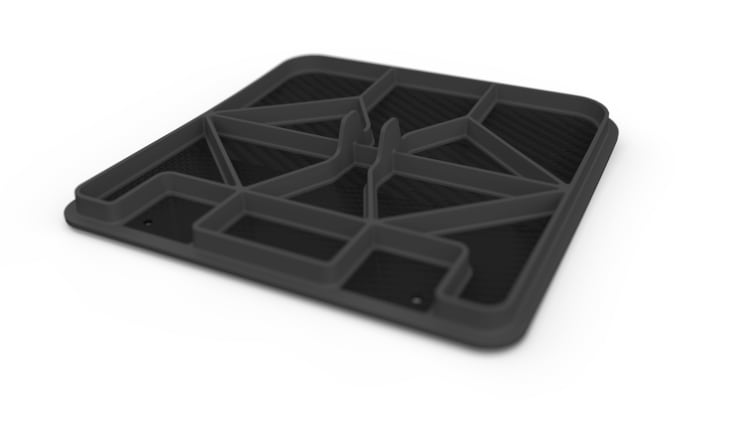
Huge potential in all fields of mobility
Developed for efficient, large-scale production, the Engel organomelt process has quickly established itself in the automotive industry, but is also attracting great interest from other sectors. "We are increasingly seeing inquiries from the aerospace industry," reports Christian Wolfsberger, Business Development Manager Composite Technologies at Engel. "In the aerospace industry, thermoset materials are increasingly being replaced by thermoplastics." The drivers of this development include cost pressure and sustainability targets. The consistent use of thermoplastic materials enables a high degree of process integration to ensure totally worry-free functionalisation of the parts; this, in turn, reduces the time taken, the raw material input and the energy requirements.