Where different material systems and several independent production steps are typically required, Engel organomelt only needs a single integrated production cell. Inspection flaps for the aircraft fuselage are the best example of this. Until now, they have been produced as thermoset sandwich parts with milled aluminium parts bolted on.
Reducing CO2 emissions is a declared goal of the aviation industry in addition to improving cost efficiency. An aircraft emits the most CO2 during its service life while it is in the air. This makes the leverage of innovative lightweight construction technologies correspondingly high, especially if these technologies can also help to close the material cycle at the end of the part's service life, and this is the case with the Engel organomelt process, which produces purely thermoplastic parts.
Engel sees huge potential for the organomelt process in aircraft production. The required quantities of structural elements and parts for the passenger cabin are continuously increasing. Further potential is opening up worldwide in the fields of urban air mobility, which includes air cabs, and logistics, where transport drones are increasingly being used.
Engel is showcasing the production of the inspection flaps at JEC World 2023 in cooperation with its customer FACC (Ried im Innkreis, Austria). The other project partners are Ensinger (Nufringen, Germany), Victrex (Lancashire, Great Britain) and Kuraray (Hattersheim am Main, Germany) for the raw materials and Neue Materialien Fürth in Germany for the part design and simulation.
Another partner company will be exhibiting in its own Expert Corner at the Engel stand. Voidsy, headquartered in Wels, Austria, is presenting an ultra-compact system for zero-contact and non-destructive material and component testing using active thermography.
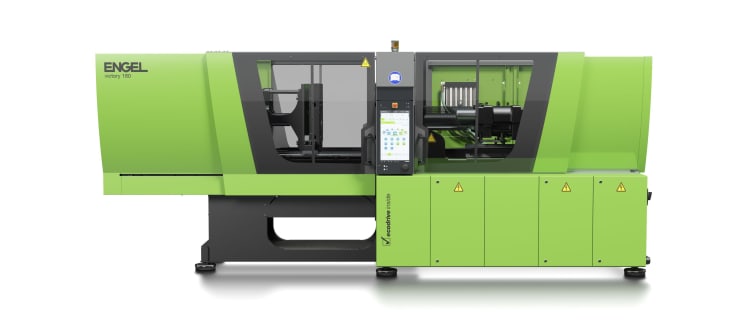
Reduced assembly overhead and labour costs
A further Expert Corner is dedicated to automotive applications with Engel organomelt. Among other things, the SPE Award-winning front-end module carrier by Lucid Motors is being showcased. Series production of the part is by ElringKlinger - headquartered in Dettingen an der Erms, Germany - and relies on the Engel organomelt process. Depending on the vehicle type, the front-end module carrier acts as a support for the charge air cooler, the headlamp modules, the wash-water tank, the horn, the distance radar module or the air intake. It also supports the bonnet through add-on bonnet locks.
ElringKlinger has succeeded in minimising both the number of pre- and post-machining steps and the costs, despite a total of 37 inserts. The extremely high level of functional integration in the injection moulding process results in lower assembly overhead, which, in turn, reduces labour costs. The front-end module carrier is used in the "Air", the first electric vehicle model by US car manufacturer Lucid Motors.
Engel at JEC World 2023: Hall 5, Stand N79