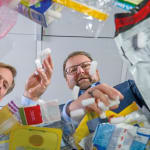
More and more companies from the plastics industry are working on improving the recyclability of plastics and thus helping to create a circular economy. One way that BASF is contributing is the ChemCycling project: At the end of 2018, the company first used pilot volumes of a pyrolysis oil derived from plastic waste as a feedstock in its own production. At a press conference in advance of K 2019, the world’s largest trade show for the plastics and rubber industry, four partners have showcased the first prototypes that were created during the pilot phase of the project.
Jaguar Land Rover (JLR), a leading automotive manufacturer, developed a plastic front-end carrier prototype for its first electric SUV, the I-Pace, out of Ultramid B3WG6 Ccycled Black 00564. "As part of our commitment to accelerate closed loop manufacturing across our operations, we are always looking for advances in technology that will help to reduce waste," said Craig Woodburn, Global Environmental Compliance Manager at JLR. "The ability to convert consumer waste into safe, quality parts for premium products through the ChemCycling process is an important step in advancing our ambition to deliver a zero-waste future."
Storopack, a globally active supplier of protective packaging and technical molded parts, used Styropor P Ccycled to make insulation packaging for temperature-sensitive pharmaceutical products as well as boxes for transporting fresh fish and protective packaging for electronic devices. "We were particularly impressed by the fact that Styropor P Ccycled can be used in food packaging. There are already various recycling options for Styropor, and ChemCycling helps raise the recycling share even further," said Storopack’s Chairman of the Management Board, Hermann Reichenecker. Storopack and BASF are thus forging a new path in the circular economy.
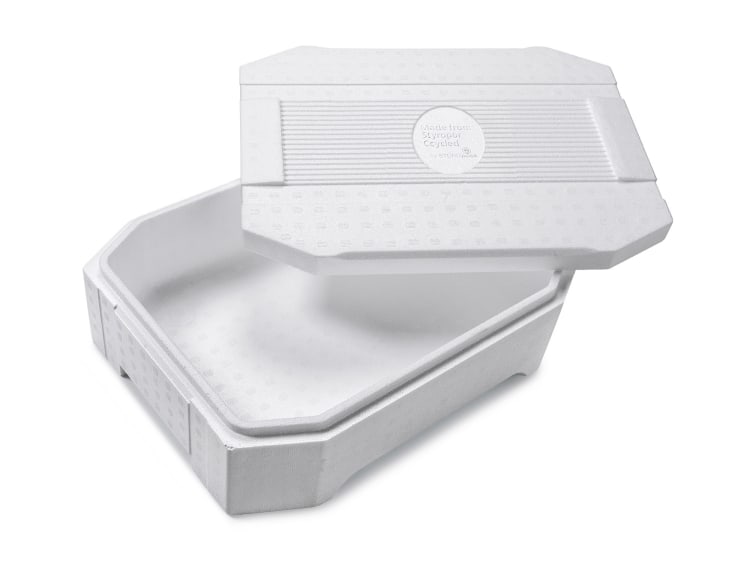
Packaging innovations made of Styropor P Ccycled from Storopack: Fishbox for food
Südpack, a leading producer of film packaging in Europe, produced a polyamide film and a polyethylene film that were processed into specially sealed packaging for mozzarella. Until now, multi-layer packaging has usually been considered to be only recyclable to a limited extent. "Film packaging must fulfill important roles: product protection, hygiene and shelf life while using a minimum amount of plastics. That is why it is made up of several materials and layers with various properties and barriers. Through innovations such as ChemCycling we come closer to solving the problems associated with recycling of flexible packaging," said Johannes Remmele, Managing Partner of Südpack.
Schneider Electric, a leader in the digital transformation of energy management and automation, manufactured a circuit breaker from chemically recycled Ultramid. "We actively assess the ability of secondary raw materials, such as recycled plastics, to meet our demanding quality standards, and stringent industry regulations and norms. We rely on BASF expertise to demonstrate the end-to-end sustainability benefits while offering an appealing cost. We are hopeful this experimentation with BASF will open room for more circular innovations in Energy Management and Distribution," said Xavier Houot, Schneider Electric’s Senior Vice President Group Environment, Safety, Real Estate.
"The pilot projects with customers from various industries show that products made with chemically recycled raw materials exhibit the same high quality and performance as products made from primary materials. ChemCycling, which uses a mass balance approach to mathematically allocate a share of the recycled material to the final product, can help our customers to achieve their sustainability goals," said Jürgen Becky, Senior Vice President Performance Materials. The certified products are indicated with the addition of "Ccycled" to their name. The prototypes presented at the press conference are part of the ongoing pilot phase of the ChemCycling project.