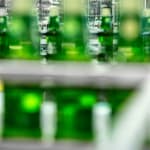
KHS and Martens are continuing to pursue their mutual strategy of reducing packaging materials. Only last year the traditional Belgian brewery invested in an Innopack Nature MultiPack machine that forms PET bottles into stable packs with the help of dots of adhesive. Martens is now planning on procuring a second NMP machine from KHS to process cans. This extension makes the brewery more flexible and thus able to meet the growing market demand for environmentally-friendly packaging. The NMP project at Martens is just one example of the ever-increasing portfolio of sustainable packaging systems engineered by the Dortmund turnkey supplier.
Martens has relied on the material-saving Nature MultiPack or NMP system from KHS since 2020, when the long-term partners began producing film-free six-packs of PET bottles for the retail trade in a joint venture. The response to the alternative to the classic shrink-film pack was extremely positive, as brewery boss Jan Martens remembers. “We were able to convince both our customers and consumers. The great demand shows that ecofriendly packaging is very popular.” The logical conclusion for Martens was thus to then also apply the tried-and-tested KHS system to its canning operations.
Martens penetrates new markets with Nature MultiPack
Thanks to the new system, in the future the Belgian brewer will not only be able to form PET bottles but also cans into stable yet easy-to-separate packs. This makes the use of shrink film or cardboard superfluous, cutting material consumption by up to 90%. “This is good for our consumers and the environment,” smiles Martens.
While the brewery uses a machine that fully satisfies its requirements with a maximum output of 54,000 containers per hour, KHS now also has an Innopack Nature MultiPack machine for the high-performance range on offer. This further developed variant can manage up to 90,000 containers every sixty minutes – or even 108,000 when running at overcapacity.
Martens hopes that by expanding its NMP setup to include cans it can penetrate new markets. “Retailers are constantly on the lookout for environmentally-friendly packaging options. I’m certain that our resource-saving Nature MultiPack solutions will attract plenty of interest,” the brewery boss predicts. His brewery now has the necessary flexibility to best meet the current needs of the retail trade.
Secondary packaging: KHS offers extensive portfolio
Nature MultiPack is just one example of the ever-increasing range of sustainable and pioneering secondary packaging systems on offer from KHS. The Dortmund turnkey supplier pursues a clear holistic strategy, as Sören Storbeck, global product account manager for packaging at KHS, explains. “Our overriding aim is to perfectly cater for all of our customers’ requirements. We thus believe in providing not just a full portfolio of line and packaging systems and solutions but also a global service network that’s available to our customers round the clock.”
Among the latest innovations engineered by the systems supplier is the Innopack Kisters wrap-around shrink paper packer (WSPP A) that can wrap cans in either paper, cardboard or film. This variety is facilitated by the modular design of all Innopack Kisters machines that enables existing models to be quickly and flexibly retrofitted with the additional paper-wrapping function. By combining various process modules, a WSPP A can process three different types of secondary packaging, for example: wrap-around cartons, trays and pads that can be wrapped in either paper or shrink film. It is now also possible to process film made of 100% recyclate on Innopack Kisters machinery – without any loss in quality or performance.
Another groundbreaking packaging alternative can be produced by the new Innopack Kisters CNP (Carton Nature Packer). This powerful and flexible packer turns cans into stable packs using toppers or clips made of corrugated cardboard or solid board. KHS’ inventiveness is by no means limited to the above. “We’re striving to develop even more efficient and sustainable systems – whether for primary, secondary or tertiary packaging,” states Storbeck. “Together with our customers and partners we’re constantly working on saving even more resources and further strengthening the recycling loop.”