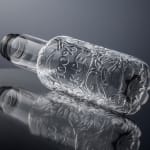
According to business magazine Forbes, around 140 PET bottles per head are circulated in Europe each year, with this figure more than twice that in the USA at 290. Despite all the criticism the plastic container is actually growing in popularity, with the number used increasing globally by around 4% per annum. Awareness of the need to recycle is also on the rise, however; according to Forbes, an estimated 57% of all used PET bottles were collected worldwide in 2019. For 2029 the magazine forecasts that this rate will increase to 68% – albeit with major differences from region to region. While 57% of all bottles could be collected in Europe, in the USA this would only amount to 30%. China, on the other hand, could become something of a model student and in ten years achieve an impressive collection rate of 82%. Collecting does not necessarily mean recycling, however: in the USA 70% of all collected plastics end up at waste disposal sites – and in Europe 30%.
Practically made for recycling: plastic
Yet plastic can be very easily recycled, especially PET. It is the only plastic that, when recycled, satisfies the legal requirements governing food grade materials. Whereas with other materials, such as polypropylene, polyethylene and polystyrene, the loss of quality which occurs on application of the usual recycling methods is irreversible, recycled PET can always be brought up to the standard of new material.
It is thus no surprise to learn that of the approximately 477,000 metric tons of PET used each year to make bottles in Germany alone, about 93% of this material is recovered and reused. Only roughly a third of this is used to make new bottles, however; the rest goes into the manufacturing of films and especially textile fibers. This means that the bottle-to-bottle recycling loop is deprived of a large percentage of this raw material.
There is also the development in price to be considered: while the cost of what is known as virgin PET is based on that of crude oil and benefits from the current low market price thereof, the charge for recycled PET has continuously risen over the last three years. Companies now have to pay about 20% more for rPET than for the original material – also because the supply cannot meet the growing demand.
High standards of quality
Not only do hurdles have to be overcome at the raw materials end; some beverage producers also have reservations. They often fear that the rPET material may discolor or that the level of intrinsic viscosity may drop. Another issue are safety standards and thus the harmlessness of the material. Time and again the question is raised as to whether multiple recycling can affect the quality. Although this has not yet been fully researched in practice, one thing is clear: as the polymer chains reform, no compromises must be made as regards the material quality as long as the additives can be completely separated off. The European PET Bottle Platform (EPBP) is just one of the institutions that helps to assure high standards of quality with its clear specifications and certifications. Whereas just a few years ago experimentation was rife and the beverage and food industries gained their experience with recycled PET through sheer trial and error, from a technical standpoint there is now nothing preventing the global use of high percentages of recycled PET. More and more beverage producers and brands are even opting to use bottles made of 100% recyclate. Where this is not yet the case, voluntary commitments are being publicized; Poland Spring, one of the biggest water brands in the USA, and Evian want to use recycled PET only by 2025. The other brands by Danone Waters, Pepsi and Coca-Cola plan to introduce a worldwide quota of 50% by this date. Their objective? They would like the consumer to interpret the slight graying that can occur when PET bottles are recycled several times over as a hallmark of quality for sustainable packaging.
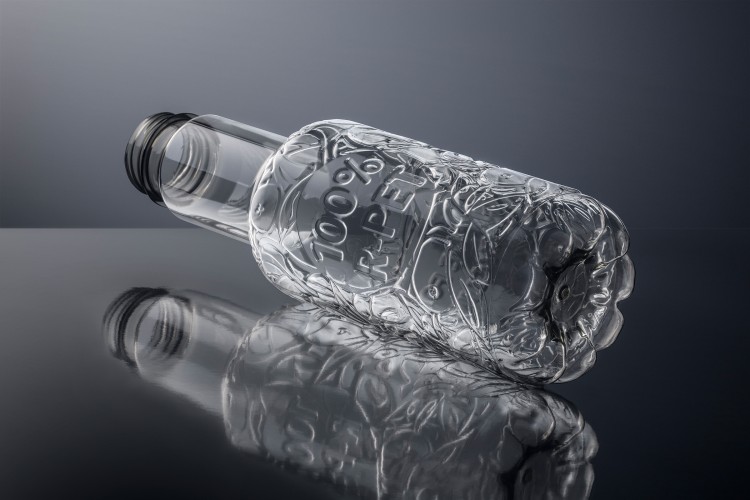