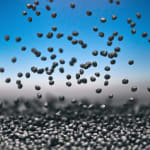
Kask, the iconic Italian helmet brand, is using expandable polystyrene (EPS) granules Neopor Ccycle from BASF for the production of safety helmets for workers. In the manufacturing process of Neopor Ccycled fossil feedstocks are replaced by pyrolysis oil obtained from recycled post-consumer plastic waste through chemical recycling at the very beginning of the BASF value chain using the mass balance approach. This way, BASF is able to offer Neopor Ccycled with a Product Carbon Footprint reduced by approximately 90% compared to conventional Neopor.
Kask is now using this more sustainable EPS to produce the internal shell of the Primero series as well as the internal shell of the Zenith X and Superplasma safety helmet series from the end of October 2024. These products feature the same high quality and safety performance and an improved product carbon footprint in comparison to using conventional EPS. By choosing these product series, which together cover the majority of helmets sold, Kask is able to make a positive impact on the circular economy.
Kask helmets setting safety standards since two decades
Celebrating its 20th anniversary in 2024, Kask has grown to become a pioneer in sport and workplace safety over the last two decades. By putting personal protection first without compromising on comfort, design and performance, Kask is setting a new approach towards head protection. Moreover, all Kask helmet series exceed the highest European and international safety standards.
“At Kask we are constantly engaged in the research and development of innovative technologies and solutions aimed to continually improving the safety, comfort and design of the helmets,” says Angelo Gotti, founder and owner of Kask. “We have the goal of enabling every worker to maximize their performance throughout the day, ensuring freedom and awareness of feeling protected even in the most challenging and risky situations.”
Neopor Ccycled from BASF contributing to preserving fossil raw materials
The decision for using Neopor Ccycled for the internal shell of Kask safety helmets has been made after intensive performance tests, which showed that Neopor Ccycled is able to guarantee the same mechanical characteristics as standard Neopor, such as all-around high impact energy absorption.
“At Kask, safety is our top priority. In our quest for more sustainable solutions, we turned to BASF to find the best materials that could ensure a lower environmental impact while maintaining the same high level of protection and comfort for workers. We are proud of this collaboration, which helps us reduce the use of virgin raw materials and support the transition to more sustainable alternatives.” - explains Marta Beltramello, Sales & Marketing Director of Kask Safety. “The Primero collection, launched in 2023, was the first to feature BASF Ccycled EPS. But we didn’t stop there: now, both the Zenith X and Superplasma collections have an internal shell made of Neopor Ccycled.”
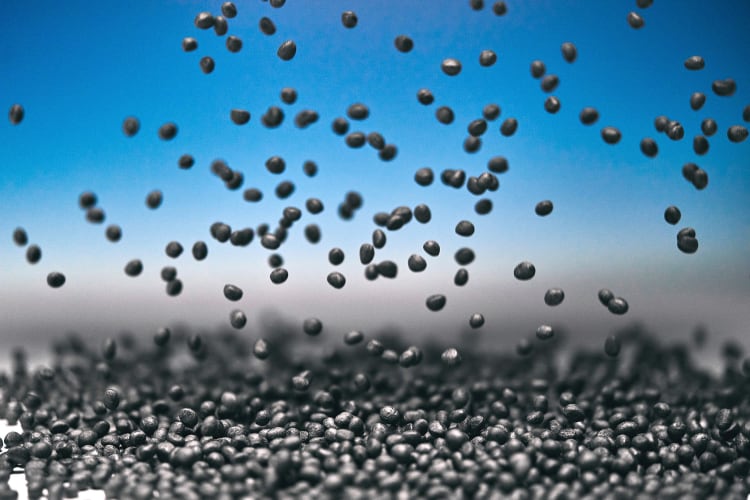
In the production of Neopor Ccycled, fossil raw materials are replaced by pyrolysis oil at the very beginning of the petrochemical value chain. This alternative raw material is obtained from pyrolysis of plastic waste that would otherwise be used for energy recovery or go to landfill. The attribution of the pyrolysis oil to Neopor Ccycled according to a mass balance approach is independently certified according to REDcert.
“It is of utmost importance for us to contribute with our products to reducing fossil resources consumption and to enabling the shift to a circular economy, while not compromising on quality or safety,” says Alessandro Gandini, Commercial Manager Styrenic Foams Mediterranean Area at BASF. “We are really proud that Neopor Ccycled has been selected for these high-quality Kask safety helmets and will help to support the safety of workers each day.”