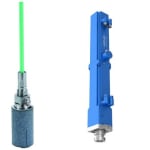
Recent years have seen the Kistler Group consolidating its global reputation as the leading provider of sensor systems by steadily expanding its product portfolio. Thanks in particular to a series of innovative developments in the maXYmos family, the consistency and continuity of these systems − as well as their simple, intuitive operation − have become familiar features of everyday industrial production. Now, at the Motek 2015, Kistler is set to unveil no less than three product innovations that will make manufacturing processes even more transparent – to increase quality and cut costs.
For years, the XY monitors in Kistler's maXYmos series have played a key part in consistent, process-integrated quality assurance: the patterns of measurement curves can be used to monitor and verify the quality of a single production step, a sub-assembly or an entire product. Now, maXYmos users can also measure multi-stage production processes (i.e. those with consecutive staggered steps): this has been made possible by equipping the maXYmos TL (Top-Level System) and the maXYmos BL (Basic-Level System) with a sequencer mode, in the same way as the successful maXYmos NC. Practical tests have shown the convincing results of this innovation: thanks to integrated sequence control, complex test processes can be mapped with no need to rely on costly external PLC programming. The programs can be set up quickly and easily with the help of the intuitive user interface on the touch display. Another advance: new evaluation objects (EOs) have been included in the maXYmos TL to support testing of additional applications such as switch testing. When the new cable extender is used, cables between TL / NC measuring modules and the display can be extended on one side, with data transmission via Ethernet. On the other side, up to eight measuring modules for different production processes can now be connected to one display.
In short: these new refinements to maXYmos now mean that optimal cycle times can also be achieved for multi-stage processes, with maximum repeat accuracy. Downtime is minimized and machine availability is increased – adding up to a remarkable increase in productivity for the manufacturing process.
But that's not all: Kistler will also unveil another member of the Joining Systems family at the Motek 2015. As well as the classical linear joining process, the new NCFR Joining Module can perform a rotary movement of the ram, either sequentially or even simultaneously. With its integrated hollow-shaft servo motors, the module features compact dimensions and extremely low weight. This design offers excellent dynamic characteristics, creating the basis for dramatically reduced cycle times. Integrated sensors continuously capture and evaluate force and displacement − as well as rotation angle and torque − with maximum precision, so 100% quality and control are ensured. The piezoelectric force sensor has two predefined measuring ranges to deliver high resolution; it also offers high overload capacity, especially in the small measuring range.
The new NCFR joining system makes mapping of complex joining processes faster and more efficient. The results: capacity utilization rates for plant are increased still further, and the commissioning and set-up phase is reduced to the minimum. And with its low energy consumption, the new NCFR Joining Module will help the automobile industry and the automotive supply sector to cut energy costs in series production.
To prove yet again that Kistler leads the sensor technology market, it will also unveil the 9240A measuring pin (a member of the strain sensor family) at Motek 2015. With its exceptionally narrow diameter of only 8 mm, this measuring pin is the perfect addition to Kistler's extensive range of strain sensors. In the majority of applications, these instruments are used for indirect force measurements on a component, as opposed to sensors that measure the force directly in the component. Depending on the design of the strain sensor, it can be positioned on the structure or mounted inside a structure. Measuring pins installed inside a structure need a cylindrical mounting bore. The advantage of these sensors is that the measuring element can be placed precisely at the point where the greatest strain occurs. Stefan Schäfer, Product Manager for Force and Strain Sensors at Kistler, explains how the new strain sensor was developed: "The development goal for the 9240A measuring pin was to offer the best possible solution for specific market requirements. This innovative new product succeeds in doing just that – so once again, Kistler has demonstrated its proximity to its customers all over the world."