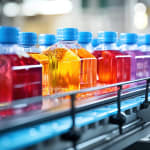
According to a survey by Global Information Inc. (a Japanese company), despite the decrease in demand for plastic injection molding during the COVID-19 pandemic, the market has now steadily recovered, reaching pre-pandemic activity levels. The main factors driving growth are population growth, the increasing prominence of sustainability issues, rising disposable incomes in developing countries, and the growth of the retail sector in emerging markets. These factors are leading to applications across various end-user industries, from bulk packaging to thin-wall containers and bottle molds.
In particular, industries such as lightweight electric vehicles and packaging materials for consumer and electronic products are experiencing increased demand, along with innovative manufacturing applications such as the delivery economy. By 2025, it is estimated that revenues from the food and beverage industry will reach USD 25 billion. Furthermore, new applications in healthcare may provide lucrative opportunities for growth in the plastic injection molding market.
Additionally, in response to the global focus on sustainable development and net-zero emissions, ESG-Environmental (E), Social (S), and Governance (G)-sustainability has become a key focus for global industrial innovation opportunities. Against the backdrop of intensifying global environmental changes and limited resources, green intelligent manufacturing is sure to be a crucial aspect for the future of Taiwan’s plastics and rubber industries.
For the plastic injection molding industry, “energy-saving strategies” were once optional, but under the impetus of global carbon neutrality regulations and trade demands, they have become a “necessity for survival.”
FCS Focuses on Value-Added Applications
In recent years, topics such as intelligent manufacturing, the circular economy, and ESG have been inseparable from innovative energy-saving and carbon-reduction solutions. Especially with the significant attention given to the new energy vehicle market, plastics have been widely used to replace steel in various automotive parts. FCS is continually assisting customers in testing the molding of various components, including those reinforced with carbon fiber or glass fiber, to meet the needs of industries such as automotive, bicycles, and even aerospace.
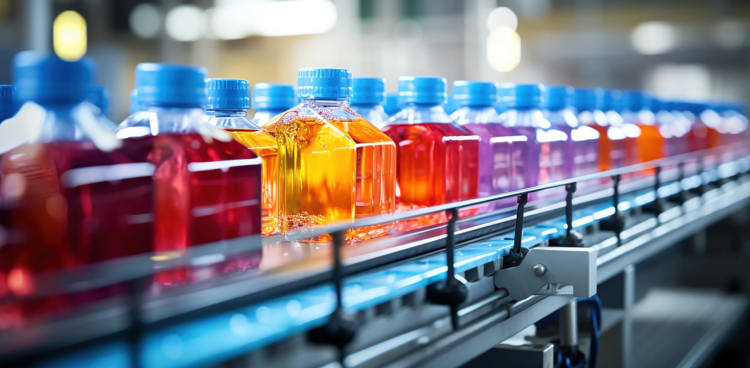
"MuCell Microcellular Foaming Technology" for Green Energy Footwear
FCS has been applying MuCell microcellular foaming technology for many years, and with the recent global focus on energy-saving and carbon reduction, it has gained increasing attention, particularly in the footwear industry. As a result, FCS has partnered with Tien Kang, one of the world’s top three shoemaking machinery manufacturers, to launch the “Gentrex Multifunctional Physical Foaming Injection Molding System” for producing thermoplastic green energy footwear materials.
Last year, with the support of the Ministry of Economic Affairs’ "Smart Machinery Industry Upgrade Program," FCS successfully passed international beta-site customer validation and entered Nike’s international supply chain with its "smart manufacturing solution for plastic injection molding of athletic shoe soles." This success has empowered FCS to serve related markets with greater confidence, receiving positive feedback and continuing to generate orders. By August of this year, nearly 40 injection molding machines had been ordered to supply footwear production bases across China, India, and Southeast Asia.
"Low-Carbon Plastic Injection Ecosystem" Collaborates with the Supply Chain to Reduce Carbon Emissions
FCS’s sustainability strategy focuses on two key aspects of energy conservation and carbon reduction: First, reducing energy consumption during the injection machine’s lifecycle by improving energy efficiency through peripheral equipment; second, replacing raw materials with recycled materials to help customers achieve a low-carbon circular economy roadmap.