In FCS’s production facilities, beyond lean production and scheduling management, they utilize smart meters for real-time monitoring and have completed carbon audits by improving high-carbon equipment such as air compressors, forklifts, and chillers. In 2023, FCS took the lead in establishing the "Green Innovation Project Team" to create the 1+10 "Low-Carbon Plastic Injection Ecosystem" project, working alongside 10 supply chain partners to collectively reduce carbon emissions.
This project involves developing a carbon reduction roadmap for the injection molding industry, focusing on three main areas: 1. smart energy optimization, 2. integration of low-carbon equipment and peripherals, and 3. development of recycled material technologies. Concrete action plans include self-conducted carbon audits, integrating energy-saving injection peripheral equipment, enhancing the use of recycled materials, upgrading energy-saving technology for new machines, and retrofitting older machines for energy efficiency.
"Smart Energy Saving + Scientific Molding" for an AI Sustainable Future
Regarding equipment energy-saving improvements, FCS will offer servo energy-saving systems, all-electric technology, power recovery systems, low-heat-loss technology, and MuCell development. Additionally, FCS will apply self-developed intelligent manufacturing technologies to help customers improve product yield, enhance carbon reduction capabilities, and, through AI fault prediction technology, increase machine utilization efficiency, thereby indirectly reducing machine carbon emissions.
Currently, FCS primarily uses the Austrian Keba control system for its injection machines and maintains close partnerships with Delta Electronics. Whether foreign or domestic brands, the industry’s development trend is closely tied to policy direction. It is hoped that major domestic system manufacturers will play a more prominent role in the government’s vigorously promoted “energy-saving + intelligent dual-axis transformation” industrial strategy, providing higher-efficiency production solutions for the equipment industry.
Generative AI applications are one of the dreams of the plastic injection molding industry. Although FCS has discussed this with experts and they believe it is still quite challenging at this stage, some basic modules may be developed first, such as accelerated solutions for stabilizing mold testing and addressing molding defects, provisionally named "Scientific Molding Guide" and "Systematic Abnormality Elimination Guide," which could benefit the industry and be prioritized for development.
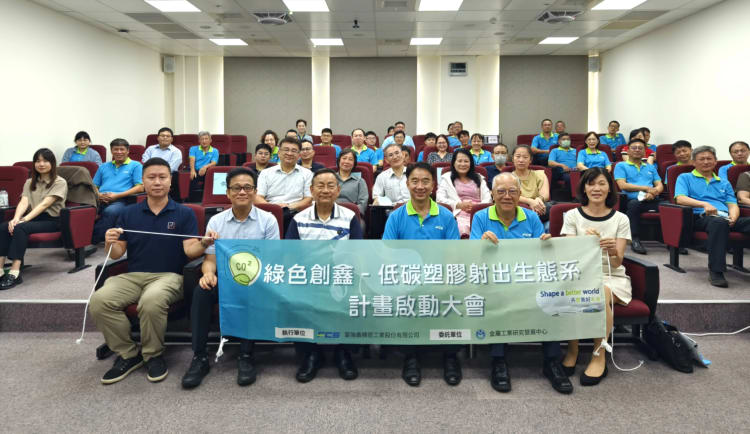
"Green Energy, Carbon Reduction/Circular Sustainability" Shines at the FCS Booth
At this year’s TaipeiPLAS 2024 exhibition in September, FCS focused on the themes of green energy, carbon reduction, and recycling, showcasing a range of applications including intelligent optics, sandwich molding, precision two-color molding, and microcellular foaming technology. These were all equipped with the self-developed iMF 4.0 intelligent manufacturing system, with four machines connected live on-site to demonstrate new achievements. Attendees were treated to innovative applications and process integrations that improve efficiency and yield, as the exhibition explored the best strategies for tackling the challenges of carbon neutrality through equipment, process technology, and production management.
The “Precision Optical Intelligent Molding System” theme includes the ultra-short energy-saving injection molding machine SA series and the ultra-precision all-electric injection molding machine CT-e series, which both produced optical goggles that could be assembled and worn on-site.
The newly launched ultra-short SA series is an outward toggle hydraulic servo energy-saving model with clamping forces ranging from 100 to 300 tons, suitable for household goods, stationery, automotive, 3C, and home appliance industries. Due to its structural characteristics, the SA can provide a relatively large mold opening stroke in a smaller space, making it popular among customers producing deep bucket-shaped products.