
With “Join our Journey” as its motto, Kraiburg TPE is calling on interested customers and partners to form development alliances. The focus is on thermally conductive TPEs, a material of the future that is currently in high demand. The aim is to develop solutions and components for the automotive and industry markets.
Benefiting from combining contrasts: Intelligent thermal management in the form of thermally conductive plastics combined with electrical insulation is capable of permanently changing current practices in many sectors of industry – leading to leaner solutions, reduced hot spots and design freedom, combined with a very high degree of process reliability in injection molding. Driven by increasing demand, Kraiburg TPE is expanding its solutions portfolio and seeking to form development-oriented alliances with customers and partners to reach the next level. The vision: Together developing superior compounds for applications with reliable, energy-efficient, durable and excellent performance.
On the basis of initial developments and tests, Kraiburg TPE has been strongly encouraged by the realization that thermally conductive plastics combined with electrical insulation will provide added value for manufacturers in the automotive sector – particularly OEMs focusing on electric mobility, as well as battery manufacturers. But the industry in general will also benefit from these solutions: Ingenious thermal management in electronics provides benefits for manufacturers of power tools, LED lights, charging stations and charging plugs, and producers of peripheral equipment and accessories for electric bikes, as well as electrics and electronics (E&E).
In similar application scenarios, aluminum heat sinks with silicones, pads and pastes have frequently been used so far, usually involving challenges in relation to processing and process reliability. As compared to these thermally conductive materials, TPEs provide thermoplastic processability that is superior to conventional methods. In addition, a TPE solution can fully exploit its strengths:
- Hardnesses range from 55 to 75 Shore A
- Various thermal conductivities of up to 3 W/(m*K) available
- Adhesion to polyolefins or polyamides using multi-component injection molding possible
- Free of PVC and silicones
Process reliability in injection molding of thermally conductive TPEs ensures that the TPE is held in place during assembly and use. With its vision of thermally conductive TPEs, Kraiburg TPE is leading the way, since a combination of adhesion to PP or PA and thermal conductivity is not yet available in the range of TPEs. “Due to an increase in the power density of systems, improved thermal management is becoming increasingly important. The future market for thermally conductive TPEs will show strong growth – and our material puts us in a good position to compete in this market,” as Martina Hetterich, qualified engineer and Project Manager for Advance Development at Kraiburg TPE, describes the necessity of the solution.
Kraiburg TPE is now calling for qualified partners who have specific project ideas and requirements as well as the ability to test and assess different TPEs.
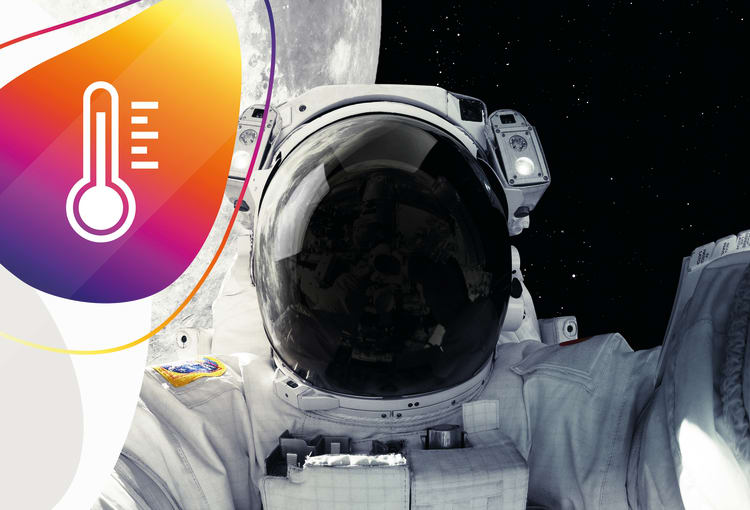