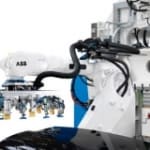
Use of thermoplastics in the RTM process
The high automatization potential of the RTM process makes it an especially attractive solution for mass manufacturing automotive components made from fiber-reinforced plastic. This technology has primarily been used to process thermoset matrix systems, such as epoxy resin, until now: "The use of thermoplastic matrix systems, which are generally more cost-effective than thermoset ones, has not been possible until now. This is mainly due to their comparably high viscosity when in a molten state, which more or less prevents pore-free impregnation of the dry semi-finished fiber products under acceptable processing parameters", explains Erich Fries, Head of the Composites/Surfaces Business Unit of the Reaction Process Machinery Division at KraussMaffei. In cooperation with Volkswagen AG and BASF SE, KraussMaffei has now succeeded in transferring the use of thermoplastic matrix systems to the RTM process.In the so-called T-RTM process, a low-viscous, reactive caprolactam system is injected into a closed, isothermally heat-balanced mold that is lined with endless fiber-reinforced semi-finished textile products, where it is then polymerized into polyamide 6. The polymerization process takes place after the fibers have been saturated, the curing time for which is very short. The first products to have been manufactured using the T-RTM process are B-pillar reinforcement prototypes made at the FRP TechCenter of the Volkswagen Group Research Center in Wolfsburg, Germany.
A basic requirement for successfully developing the T-RTM process was comprehensive adaptation of the caprolactam systems currently in use. In addition to the required activator and catalyst, they also contain a number of additives and admixtures, which are later used to form the matrix systems adapted to FRP components. A special metering machine specifically adapted to processing the extremely low-viscous system was also required to ensure that the manufacturing process runs smoothly. The mixing and metering machine used by KraussMaffei is therefore fitted with a special mixing head, high-performance axial pumps and a fully electric temperature-control system.