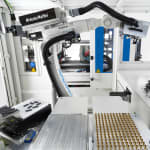
"Efficiency meets sustainability" is KraussMaffei's motto at the Fakuma trade show in Friedrichshafen, Germany (October 12-16, 2021; Hall A7, Booth No. 7303). Front and center are cost-effective system solutions for medical technology, logistics packaging, technical appliances and lightweight construction, which allow for a measurable increase in efficiency and sustainability, for example through the use of high percentages of recycled material.
"As a comprehensive solution provider, our goal is to support our customers sustainably in achieving business success. We combine our machine and application technologies with suitable digital solutions and products to generate clear added value for our customers along the entire value chain," says Dr. Volker Nilles, Executive Vice President of the New Machines division at KraussMaffei. Consequently, the solutions presented at Fakuma are completely geared toward "Efficiency meets sustainability" and have a clear focus on output maximization, high product quality, reduction of life cycle costs and ensuring sustainability.
This year, KraussMaffei has made the conscious decision to have an all-digital presentation at Fakuma. "Since the situation has become challenging due to the COVID pandemic, we decided on this kind of trade show appearance early on and used the time to strengthen contact with our customers through digital Pioneers!Talks, road shows and personal conversations. Directly after Fakuma, we are planning further local Pioneers!Table events for our customers in Europe," says Nadine Despineux, Executive Vice President of the Digital and Service Solutions division.
Level up your technology – More efficiency and sustainability in injection molding and in reaction process machinery
Efficiency and sustainability are the focal point of the system solutions of Injection Molding Machinery, Reaction Process Machinery, Automation and Digital Solutions. Wherever large logistics packaging materials are concerned, such as pails, boxes or pallets, plastic processors benefit from higher outputs thanks to the high plasticizing capacities of the MX and GX series from KraussMaffei. The BluePower technology ensures excellent energy efficiency. Furthermore, the APC plus machine function permits safe processing of high percentages of recycled material. The shot weight remains constant at all times. The outcome is an extremely high yield of good parts of up to 100 percent, without production interruption.
In the Medical Technology business area, KraussMaffei demonstrates – using the example of a micromembrane like the ones currently used for vaccination doses – how to implement the processing of liquid silicone (LSR, Liquid Silicone Rubber) successfully, safely and cost-effectively, even in micro-injection molding. The application on the PX 25 SilcoSet is cleanroom-compliant according to class ISO-7 in accordance with DIN EN ISO 14644-1 and allows for high shot weight consistency, thus maximizing the yield of good parts thanks to APC plus. The high degree of automation and the data transparency throughout the process ensure cost-effective and safe production.
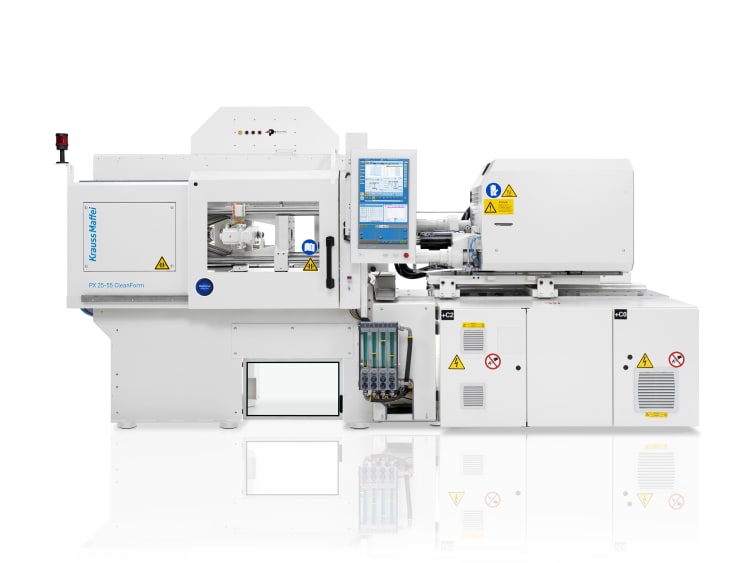
Micro-injection molding with high precision using liquid silicone: The PX 25 CleanForm for manufacturing micromembranes for vaccination doses in medical technology
In the business of Technical Appliances, KraussMaffei demonstrates – using the example of an intricate connector with four metal inlays – how an advanced, completely tested and ready-to-install component can be realized at low part cost. The all-electric injection molding machine PX 161 with matching automation offers maximum precision while taking up minimal space as a result of the space-saving integration of the automation, high efficiency in the placement and overmolding of the metal parts as well as an extensive inspection routine.
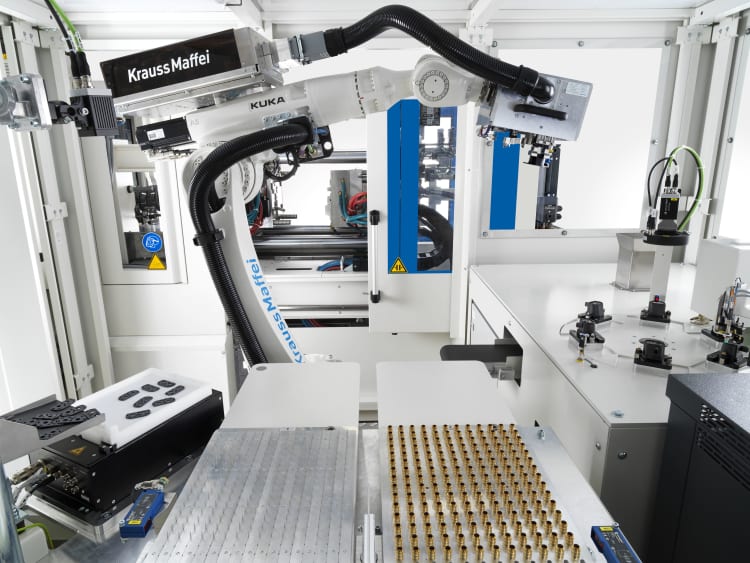
Complex connector fabrication made easy: The injection molding machine with docked automation cell embodies maximum precision with minimum footprint
More efficiency in PUR processing and lightweight construction
The RimStar Smart mixing and metering machine embodies higher efficiency in PUR processing. Coming with requirements-based equipment options, it brings exactly the right technology at the highest level of quality for series production as well as for small batch sizes. This means users can offer their customers new products at low part costs. The footprint of just 4.8 m², the excellent price/performance ratio and the user-friendly concept make production with the RimStar Smart particularly efficient and sustainable. The high quality of the components ensures process stability and high availability.
With the motto “all the steps in one”, KraussMaffei will be demonstrating at Fakuma how production processes for complex composites lightweight components can be more efficient, from the concept all the way to series production. KraussMaffei has technologies for the complete production chain for plastic components, from foaming, fiber composite and injection molding to moldmaking and component post-processing. This extensive expertise allows KraussMaffei to provide complete manufacturing solutions that are cost-effective and sustainable at the same time.
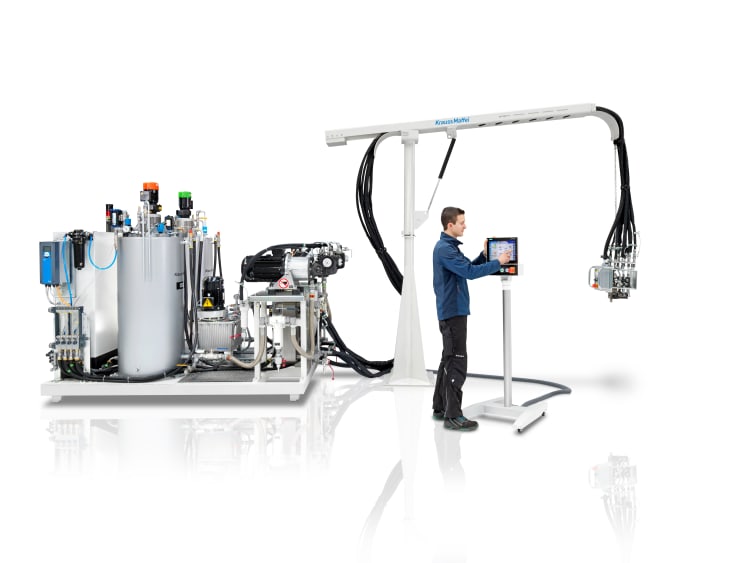
Mixing and metering polyurethane in limited space: The RimStar Smart pumping machine requires only 4.8 m² for its core components.