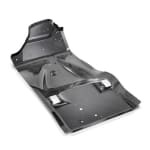
Development focuses primarily on creating processes and systems that can be used to manufacture lightweight components in large series production, for which there is great demand in vehicle construction. "We will demonstrate our expertise at JEC in many up-to-date application examples. In doing so, we will prove that we offer our customers the right process for optimized production for all corresponding component requirements," emphasizes Erich Fries, Manager of the Composites/Surfaces business unit at KraussMaffei.
Wet-embedded fibers
One of these groundbreaking technologies for manufacturing high-performance components based on carbon-fiber reinforced plastic (CFRP) is called wet molding, also known as wet pressing. In comparison to classic RTM processes (resin transfer molding) like HP-RTM (high-pressure RTM) and C-RTM (compression RTM), wet molding is characterized by a simpler process chain in which the preform process is omitted completely. For this reason, wet molding is a cost-effective alternative for manufacturing new lightweight components in vehicle manufacturing.During the wet molding process, a mixing head applies the resin (usually epoxy resin) onto the flat-lying semi-finished fiber product in continuous strips. The fiber product is then passed on to the mold, where it is compression molded. This process has two decisive advantages. It saves valuable cycle time, because the resin can be applied to one component at the same time that the other is curing in the mold. The system can also be more reactive. Charging is no longer necessary in the heated mold, in which a reaction cannot yet occur. These two factors save time, leading to shorter cycle times. It is also possible to use recycled fibers. This makes wet molding an excellent option for industrial processing of recycled fibers in the RTM process.
KraussMaffei wet molding lines are also characterized by a high degree of automation, ensuring short cycle times and high numbers of pieces. At JEC World in Paris, KraussMaffei is presenting current application examples from the mass production of the new 7 series BMW and the i8 electric car.