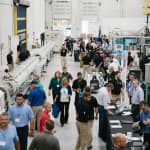
Milling, ultrasonic cutting and deflashing, as well as testing or flexible ultrasonic welding (depending on the selected equipment) in a compact post-mold processing plant: With this technological innovation, KraussMaffei is highlighting its extensive expertise in delivering complete, highly automated production systems for preparing, producing and post-processing of foamed multi-component PUR components. Note: For the first time, KraussMaffei will demonstrate the fully automatic deflashing of semi-rigid foam components with a robot-controlled, deflashing head developed in-house as well as an end-to-end system for process monitoring and data analysis.
Process know-how, design expertise
Efficient production of premium quality foamed interior components can be achieved by coordinating and digitally connecting all process steps. In this case, KraussMaffei can offer the entire process chain from a single supplier. This chain includes skin spraying and precise scoring of the decorative film in the airbag area as well as activation of the substrate surface. For backfoaming of the decorative film, the technology leader offers a high-end portfolio of mixers and metering machines for PUR processing that meets all requirements. The substrates also come from an injection molding plant from KraussMaffei if required.
New all-rounder: Three robots add the finishing touches simultaneously
For the final post-mold processing, efficient punching machines or multi-functional robot systems are available. Milling, ultrasonic cutting, deflashing, testing or flexible welding tasks can now be carried out with a single, mobile machine concept for finishing components. The new MultiStar processing cell uses up to three robots operating simultaneously with different tools. A component positioner developed by KraussMaffei with quick-change capability for product pickup eliminates the need for any manual setup. The component is placed in a safe, steady position which is optimal for processing. This positioning provides the basis for high quality in processing.
Innovation: Semi-hard and hard foams can be deflashed fully automatically
Another new feature is the fully automatic deflashing of semi-rigid foam components. The newly developed technology with a deflashing tool and innovative design increases efficiency, while stable process control ensures consistent high post-mold processing quality. Thanks to the selective removal of foam flash, the foam body is undamaged. The technology is not only suitable for deflashing foam components, but can also be used in other areas of plastics processing, such as plastic injection molding or certain composite applications.
Source: Krauss Maffei