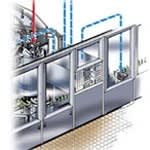
Clients can then use this monobloc to run all the labelling processes in common use, thus enjoying enhanced flexibility. Whether it’s cold-glue, pressure-sensitive, hotmelt or also shrink and stretch sleeves – with the Krones DecoBloc, all these labelling processes can be speedily performed.
The docking stations feature motorised height adjustment, so that irrespective of the floor level involved the labelling stations can be swiftly prepared for a product change-over at the touch of a button. Different machine sizes offer outputs of up to 72,000 containers an hour. Servomotors are used to ensure maximally accurate dress positioning. For sleeving applications, moreover, there is a choice between shrink-sleeve labels with a downstream Shrinkmat tunnel or stretch-sleeve labelling. There is also an option for camera-based alignment of the containers on an embossed marking or a container contour, thus ensuring that the labels or sleeves are optimally positioned in relation to the bottle. So that’s well-nigh full-coverage functionality.