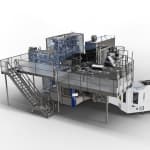
A sterile process chain from preform sterilisation to sealing - this summarises the principle of the Contipure AseptBloc. A system that has proven its worth: At Krones, almost 90 per cent of aseptic fillers are currently integrated into this block solution. While this type of system was previously used primarily in the medium and high output range, there is now also a compact version that can be used to economically fill outputs as low as 8,000 containers per hour.
The basis for expanding the portfolio was laid by a further development in stretch blow-moulding technology: two years ago, Krones launched a new generation of its Contiform blow-moulding machine, which for the first time also enabled configurations of four, six and eight cavities. Similarly, the filling technology team further developed its existing aseptic filler, also with a view to low outputs - and finally combined both systems in a compact version of the Contipure AseptBloc.
The small footprint of the block is particularly noteworthy: the smallest version contains a four-cavity blow-moulding machine and a filler with a pitch circle of 1,080 millimetres - and currently only requires around 100 square metres of installation space - with potential for further space savings. This extremely small footprint can be achieved, for example, through a revised cleanroom concept, optimised positioning of peripherals such as media supply or valve manifolds and integration of the piping directly into the system. "Thanks to its well thought-out layout, the compact version of the Contipure AseptBloc is ideal for those companies that have little space available in production - whether installing a new line or modernising the blow-moulder and filler in an existing aseptic system," says Thekla Osswald, who is leading the project on the Research and Development side.
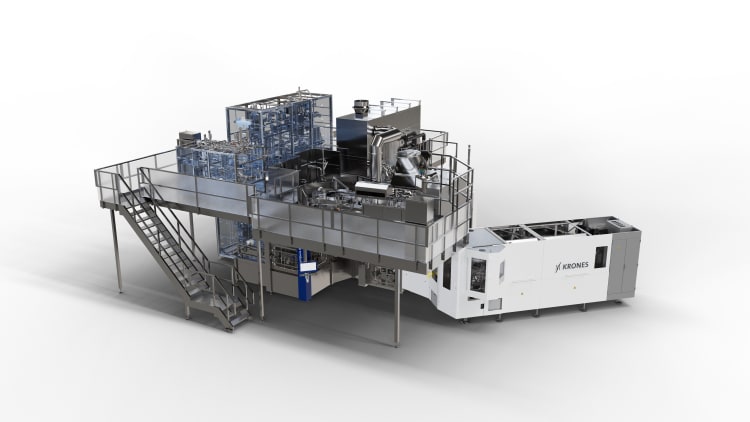
Ideal for juice, milk or plant-based milk alternatives
Apart from the space requirement, the compact version of the Contipure AseptBloc is in no way inferior to the tried-and-tested standard version: Here too, only one sterilisation medium is used, namely gaseous hydrogen peroxide. Furthermore, since the preform and not the bottle is sterilised first, lightweight containers can also be used. Compared to conventional aseptic processes with container sterilisation, the Contipure AseptBloc enables material savings of around two grams per bottle.
And as usual, the compact version of the Contipure AseptBloc is also suitable for a wide range of different product categories: Whether distributed at ambient temperature or within the cold chain, whether in the low- or high-acid range, whether with or without chunks of up to 5 x 5 x 5 millimetres - all non-carbonated beverages such as juice or dairy products can be processed on the system. And lightweight containers too.
The smallest version of the advanced Contipure AseptBloc incorporates a Modulfill Asept filler with a pitch circle of 1,080 millimetres, enabling up to 20,000 containers per hour to be aseptically produced, filled and sealed. The Krones filling technology team is currently working on further models of the compact version in order to close the gap between the 1,080-millimetre version and the familiar standard lines.