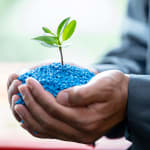
The specialty chemicals company Lanxess is one of the world’s first plastics manufacturers to offer its customers - processors of its Durethan polyamides and Pocan polyesters (PBT) - certified values for the carbon footprint of the base resins. Certification was done by an accredited verification body and includes not only the polyamide 6 precursor caprolactam but also the glass fibers manufactured by Lanxess in Antwerp. Glass fibers are used for reinforcing plastics if necessary.
"These certified values enable our customers to more accurately estimate the climate-friendliness of their products and identify ways of further reducing their CO2 emissions," says Guenter Margraf, Head of Sustainability and Product Management in the High Performance Materials business unit. "The values are also an important part of life cycle analyses, which are increasingly being used in the automotive and electrical and electronics industry to systematically analyze how products impact the environment from manufacturing through to disposal."
Standardized cradle-to-gate analysis
The values were calculated according to the standard ISO 14067:2018 for the carbon footprint of products. The analysis factored in all the major emissions that occur up to the point at which the product leaves the Lanxess factory gate (cradle-to-gate). These include not only direct emissions (scope 1) but also indirect emissions from the purchase of energy (scope 2) as well as the emissions that occur in the upstream supply chain, for example those associated with the raw materials used and transportation processes (scope 3).
"We were especially pleased to learn that, with 3.66 metric tons of CO2 equivalents emitted per metric ton of polyamide 6 produced, the carbon footprint of our polyamide 6 base resin is much smaller than the current published European industry average," says Margraf. One reason for this is that Lanxess synthes the plastic in a highly integrated plant network at its Antwerp site. From 2024 onward, the carbon footprint of polyamide 6 production is set to improve significantly yet again when, in 2023, if all goes to schedule, Lanxess will be opening a second nitrous oxide reduction facility in Antwerp. "Reducing nitrous oxide cuts the direct emissions associated with polyamide 6 production by almost 90%," says Margraf. Lanxess is also looking to use sustainable raw material sources for Caprolactam with a view to reducing the carbon footprint of its polyamide 6 to less than three metric tons of CO2 equivalents. The certification also revealed that the carbon footprint of the PBT base resin from Lanxess was less than that of many other manufacturers.
In glass fiber production, Lanxess also has a significantly smaller carbon footprint compared with most of its competitors. "This applies in particular to our resource-efficient Eco glass fibers, which, with a carbon footprint of 0.4 metric tons of CO2 equivalents per metric ton of glass fiber, save more than 70% of emissions compared with the published industry average. We use industrial glass waste in our production, which reduces the consumption of raw materials and energy and avoids waste," says Margraf.
Lower emissions thanks to more sustainable raw materials
Lanxess is looking to use the certified carbon footprints for identifying ways to reduce the level of greenhouse gases emitted during plastic production. One focus is on the use of sustainable raw materials due to the significant leverage effect that can be achieved here. New product ranges such as Durethan Blue, Durethan Eco or Pocan Eco are currently being extended that contain a significant proportion of circular (recycled or bio-based) raw materials or have a carbon footprint that is considerably smaller than conventional products. The sustainable origin of those raw materials is certified according to the ISCC Plus standard ("International Sustainability and Carbon Certification"). The certification is coupled with mass balancing, which allows the share of sustainable material in the end product to be determined and subsequently indicated in a transparent manner for processors. One product example is the 60%-glass-fiber-reinforced Durethan BLUEBKV60H2.0EF. In this polyamide 6 compound, 92% of the raw materials have been replaced by sustainable alternatives.
Carbon footprints to be available for compounds
Lanxess is now planning to calculate the carbon footprint associated with the compounding of polyamide and PBT (engineering plastics). "We are collaborating closely with our suppliers to not only calculate the carbon footprints of the different compounding raw materials but also leverage further potential for cutting emissions," says Margraf.
The certified carbon footprint as well as the mass-balanced Eco and Blue product ranges will take center stage for Lanxess at the plastics trade show K 2022 in October (booth C76 - C78 in Hall 6).
Lanxess wants to make its entire supply chain climate-neutral
In August 2022, the specialty chemicals company announced its mission to make its upstream and downstream supply chains climate-neutral by 2050. This encompasses indirect emissions associated with purchased raw materials in particular, but also emissions associated with its logistics processes and end products. By 2030, the aim is to cut scope 3 emissions by 40% compared with the reference year 2015. For direct emissions in production (scope 1) and energy sources (scope 2), Lanxess announced three years ago its intention to achieve climate neutrality by 2040. The renowned Science Based Targets initiative has validated these targets and confirmed that Lanxess is doing its bit to limit global warming to no more than 1.5 °C.
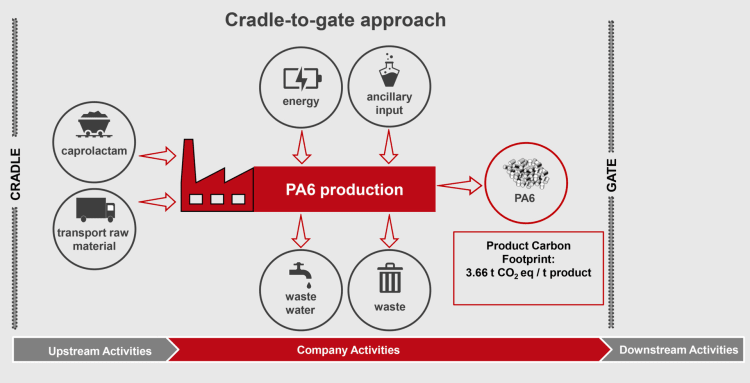