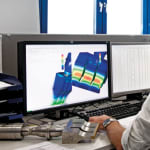
As well as the simulation, the precise surveying of the sonotrode is also a decisive success factor. All natural frequencies (modes) with their typical vibration forms are surveyed by means of laser scanning vibrometers. This allows direct adjustment in accordance with the simulation. In oscillating condition, the amplitude is highly accurately checked at all the points that are relevant for the weld – it is not rare for this to include 50 different measuring points. The process demands in-depth knowledge of ultrasonic acoustics.
Another step in technical progress is the new software functions of the fully digital generators, which make it possible to run complex sonotrode geometries. The acoustic input signals of large-sized sonotrodes can be optimally adjusted. A precondition of this is that the ultrasonic converter converts these high-frequency electrical signals into mechanical vibration with no quality losses.
Surgical instrument handle: three-dimensional surface with height difference
A weld tool is being developed for an American medical customer, to join the battery-operated handle of a liposuction instrument. This was presented for the first time at Medica 2015. Difficulties were posed by the size of the plastic handle and by the complex surface, with height differences of up to 12 mm in the joining area. Mapping the negative of the component contour on the weld tool, with a surface of 220 mm × 180 mm, and causing it to oscillate evenly is a masterpiece of vibration technology.Fig.1. Sonotrode for the welding of a plastic handle on a liposuction device.
Fig.1. Welding contour of a plastic handle of a liposuction device.