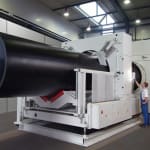
Major reason for UPI’s decision was the complete line concept. Battenfeld-Cincinnati’s greenpipe system which integrates optimized technologies for large diameter pipe extrusion, including the new 40 L/D high performance single screw extruder solEX, the inner pipe cooling concept enabled by the helix-pipeheads and the energy efficient downstream with a swarfless cutting unit for very large wall thicknesses.
UPI extends its leading market position in the Gulf region with large diameter pipe extrusion lines for 1200mm, 1600mm and now 2000 mm diameter. All 3 production systems are supplied by their preferred supplier, Battenfeld-Cincinnati.
For many years, Battenfeld-Cincinnati has been the leading provider for extrusion lines for large diameter polyethylene pipe up to 2500mm.
This year, already 10 international customers from Asia, Saudi Arabia, Egypt, Great Britain and Germany have chosen complete large diameter pipe extrusion systems from Battenfeld-Cincinnati. Continuous advancements using the technology resources within the Infrastructure division have lead to unique improvements in large diameter pipe extrusion lines. In addition to innovative cooling of the inner pipe surface utilizing an engineered pipe head cooling system, today’s complete line systems, named greenpipe, are available combining maximum productivity and energy efficiency.
Battenfeld-Cincinnati’s greenpipe lines are equipped with the new high performance 40 L/D single screw extruder solEX. The solEX extruders feature 15% less energy consumption and outputs that exceed conventional same size 30 L/D extruders by 85 to 125%. Pipe heads executed as EAC- (Efficient Air Cooling) or KryoS-model, enable a reduction of the extrusion line cooling length by up to 50% providing additional energy and cost savings.
This efficiency is realized by an engineered cooling system within the pipe head. Due to the efficient cooling system, the downstream’s energy consumption, compared to conventional technology, is reduced up to 50% with the special greenpipe downstream solution. The greenpipe downstream equipment has a central cooling water inlet that supplies all cooling tanks in a reverse cascade configuration. Battenfeld-Cincinnati additionally offers high-performance haul-offs and cutting units enabling an optimal combination of all line components from a single source.
Plastic pipe has a leading acceptance position in applications due to their performance property advantages compared to concrete and metal pipe. With growing global population, industrialization and urbanization; the demand for water supply networks continue to increase. This demand will continue to drive the need for large diameter pipe. Battenfeld-Cincinnati’s leading solutions with greenpipe technology provides manufactures with the highest performance and energy efficient large diameter pipe production systems.