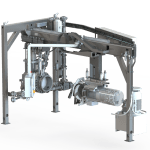
At Plast in Milan, Italy, from September 5-8, Maag Group shows integrated solutions for the processing of polymers in the recycling process in hall 13, booth B31, in particular the Eco 500 high-performance melt filter from Ettlinger.
Maag Ettlinger's Eco 500 is a high performance melt filter for the filtration of heavily contaminated polymer feedstock. For chemical recycling, this technology is outstanding for filtering low viscosity polymers. The filter is self-cleaning with a rotating, perforated drum, through which there is a continuous flow of melt from the outside to the inside. A scraper removes the contaminants that are held back on the surface and feeds them to the discharge system. This enables the filter to be used fully automatically and without any disruptions over long periods without having to replace the screen. The advantages: Reliable melt filtration, ultra-low melt losses constant pressure curve, fast spreading of the contamination and short residence time of the melt in the filter.
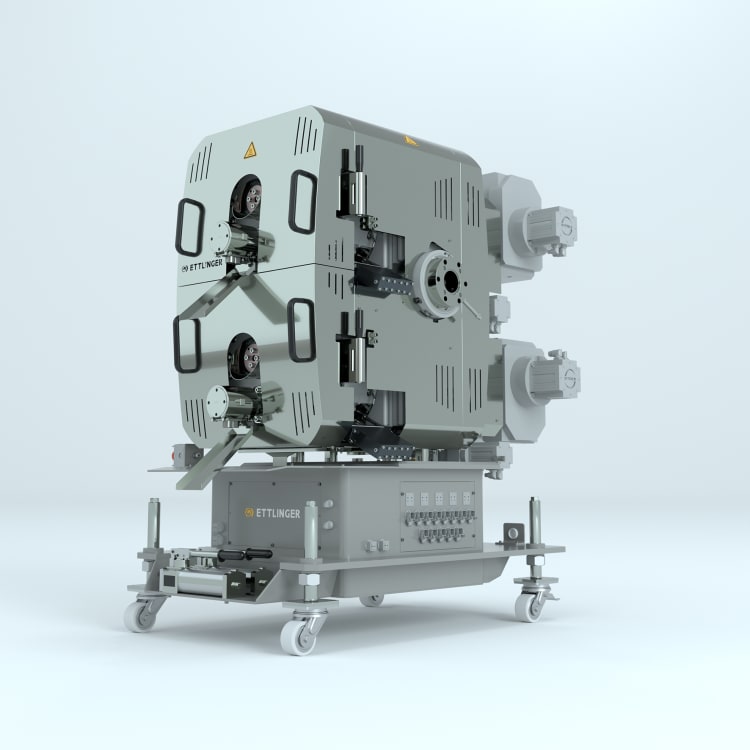
Maag Ettlinger's Eco 500 high performance melt filter
Pearlo 350 Eac with liquid-heated die plate for high capacities:
The underwater pelletizing system Pearlo 350 Eac is especially designed for high throughputs of like 18.000 kg/h of Virgin Polymer production. The unique cutting blade design and optimum water and material flow conditions within the cutting chamber provide not only ideal and homogeneous cooling effects but also outstanding pellet quality. Another innovative design feature of the Pearlo is the cutting blade advance system, which permits axial movement of the cutter shaft resulting in a precise blade advance as well as a regrinding of the blades during production. This allows higher equipment availability, elongated production runs and thus saves costs.
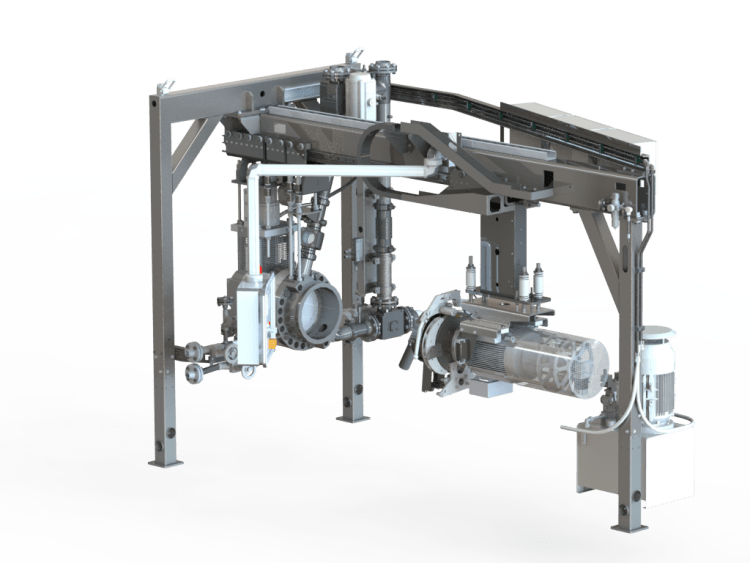
Maag Group Pearlo 350 Underwater Pelletizer
Under the name Ebg, Maag is presenting a strand pelletizing system for highly filled, hydroscopic and water-sensitive compounds. Ebg scores with a high degree of automation, gentle material processing and excellent product quality. From the die head to the granulator, the pelletizing system forms a unit that, despite its compact design, has features of a large compounding system. Automatic feeding in case of strand breaks, removal of melt residues on the die plate by the patented Hot-Air-Knife and synchronization between conveyor belt and strand granulator to name a few. Also, in this machine the control system has been revised and now allows the operator to read out the machine status live via Bluetooth.
All Maag Group extrex gear pumps in x6 class design are completely re-engineered and have redesigned components, from the shafts through to the bearings and seals, and optimized the interaction of the components. Specially developed gear teeth with low compression allow very high pressures to be achieved with low shear rates. The result is a further increase in achievable product quality, volumetric efficiency, as well as production consistency and safety.
For more information on our products, visit www.maag.com.