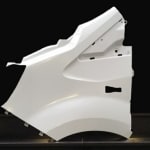
On May 20 GAZ manufacturing plant started production of dropside and all-metal trucks with 3,5 tons fully loaded mass. The new model has over 50 engineering and technological changes. Among them are polymer compound splashboards with addition of carbonic nanomaterials. This hi-tech material developed by R&P Polyplastic offers all necessary physical and mechanical properties. Exterior parts produced from this material can be painted on electrophoresis lines.
The first Russian polymer nanocompound for injection molding has been created basing on domestic polyamide 6. The material fully complies with the automotive industry requirements on electroconductive and physical and mechanical properties for production of exterior parts.
"We are very proud to make our contribution to the technologic advance of the Russian auto industry. GAZ is the first domestic car manufacturer to use polymer compounds for production of exterior parts. This process is cheaper than sheet metal stamping. The problem was that even having required strength properties they were inconsistent with volume resistivity indications necessary for painting body parts in line. A separate line was required, which made the process economically unviable. We managed to solve this problem: electro dispersive compounds with carbonic nanomaterials enables to paint the whole car body in line", – says Mikhail Katsevman, Head of R&D at R&P Polyplastic.
Nanotechnologies allowed to radically change polyamide properties with respect to its electroconductiveness: time-constant insulation resistance level amounts to 106–108 Ω∙сm, while the required physical and mechanical properties are preserved.
The first prototypes of splashboards were produced in the end of 2020. In February 2021, specialists of R&P Polyplastic together with the GAZ molder launched the preproduction stage: a large batch of polymer nanocompound for production of splashboards of the preproduction Gazelle was manufactured.
Predictions as of the start of serial production of nanocompound splashboards were conservative. R&P Polyplastic was hoping to start mass produced supplies in the second half of the year however the parties managed to finalize all processes ahead of schedule.
In the future NN platform will be used for creating a whole range of new-generation vehicles of 2,5 – 4,5 tons weight class designed for national and export sales.
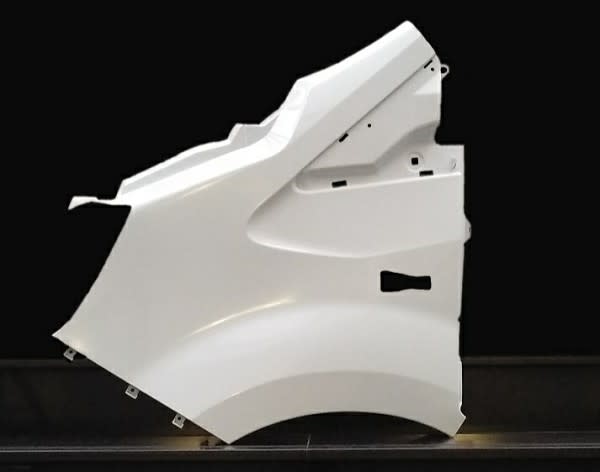