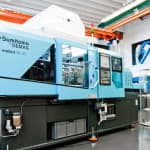
The Spanish agency of the German-Japanese machine manufacturer Sumitomo (SHI) Demag will be demonstrating the performance capabilities, precision and reproducibility of its IntElect and El-Exis SP machine series to the expert visitors.
The smallest model in the IntElect series, an IntElect 50-45 with 500 kN clamping force, will be manufacturing control knobs with a diameter of 3.5 mm from polyacetal (POM) for hearing aids in a cycle time of 10 seconds at Equiplast 2011. The light parts, weighing only 10 milligrammes, and the shot weight of only 280 milligrammes set high quality demands and require absolute reproducibility. The IntElect, with its precise and sensitive drives and the removal system which is integrated into the machine, fulfil the special requirements of zero-defect production.
Sumitomo (SHI) Demag has designed and created the production cell in collaboration with several partner companies: the 4-cavity cold runner mould with tunnel feed was deigned and constructed by Stamm AG, Hallau/Switzerland. The well-established mould manufacturer and injection moulding business has long specialised in the production of especially demanding micro-parts made of the most varied plastics. They employ many machines from Sumitomo (SHI) Demag for this purpose.
The cabin conforming to clean-room standards and the laminar flow unit controlling the production system originate from the company of Max Petek Reinraumtechnik, Radolfzell. The Filter Fan Unit (FFU) of the laminar flow unit cleans the sucked-in external air, provides a consistent, laminar air flow throughout the mould installation space of the machine, ensures clean-room classification ISO 7 is adhered to in the corresponding production environment and prevents particle penetration.
As a specialist in automation solutions, MAi GmbH & Co. KG, Küps, integrated the six axis robots made by Yaskawa Europe GmbH into the injection moulding machine, the casing for which on the non-operator side has been widened by only 200 mm. The robot is anchored suspended to the fixed tool platens. This design keeps the clean-room compact, the amounts to be moved small, the strokes of the robot short and the danger of contamination of sensitive parts on the way from the removal of parts to packaging via inspection low. The control knob will be subjected to a fully automatic 100% optical check while still inside the clean-room cabin.
IntElect smart equipment for clean-room production
With its IntElect smart, NC5 control and comprehensive catalogue of options, Sumitomo (SHI) Demag offers injection moulders a flexible and economic machine design from the electric machine series modular system. Due to numerous equipment features, the IntElect 50 is already set up at the standard required for use in producing medical plastic parts. It provides large tie-bar distances, linear guides for maximum parallelism for tool platens, excellent reproducibility with outstanding processing capability values as well as high reliability and availability.
These properties rank as the basis for the zero-defect production of medical and medical engineering precision parts. The comprehensive preparation of the machine to present special options offers the highest level of flexibility with customised equipment.
The IntElect 50-45, as the central component of the production system at Interplas, is equipped with a 14 mm screw for the plastification of small amounts of material for small shot weights. The patented, switchable activeLock nonreturn valve closes with a short abrupt turn counter to the plasticising direction prior to the injecting of the melt runners of the nonreturn valve. In this way, it provides a very small and residual mass cap in front of the screw which remains consistent over many cycles.
This contributes towards a high process consistency being achieved and ensures consistently high product quality specifcally with precision parts and very small shot weights such as the hearing aid component. Together with the seamless monitoring of the processing forces during the mould movement by the quickly reacting NC5 machine control, the highly sensitive activeQ mould protection system provides effective protection for valuable moulds against wear or damage.
Like all of its electric injection moulding machines, Sumitomo (SHI) Demag manufactures the IntElect smart at its centre of competence for electric machine technology in Wiehe, Thuringia. It is programmed with eight clamping forces ranging from 500 to 4,500 kN.