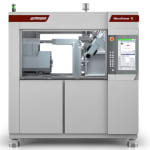
Through the combination of the high precision 2PP µ-3D printing and the performance of the Micropower 15t micro injection molding machine from Wittmann Battenfeld, NanoVoxel has successfully reduced the fabrication timeline of high precision micro-parts to two weeks. Integration of these micro-manufacturing methods allows for swift prototyping and opens new possibilities in engineering and design across industries. With initial applications in biomedical and consumer electronics, the breakthrough includes the production of intricate microparts with unprecedented accuracy and design freedom. NanoVoxel, based in Austria, has innovated this approach that marks a significant advancement in the landscape of efficient and customized micromanufacturing.
High precision microparts are finding increasing relevance in different sectors including biomedical, consumer electronics, and many others. Most of the applications being developed require designs that require high precision, fast iterations, and challenge conventional design freedom.
For example, current manufacturing methods such as CNC, EDM, mask-lithography, and SLA 3D printing struggle to quickly or precisely produce parts like micro-diffusors for acoustic applications featuring 70 µm 3D details; micro-lenses with a roughness below 10 nm; micro-needles with 5 µm tips; micro-nozzles with apertures under 20 µm; and micro-fluidic chips with specialized filters.
However, this is made possible when two advanced technologies in micromanufacturing are combined: 2PP µ-3D printing and micro-injection molding. This expertise is NanoVoxel´s forte, a start-up founded in Vienna in 2022 to disrupt the industry standard of such micro-components.
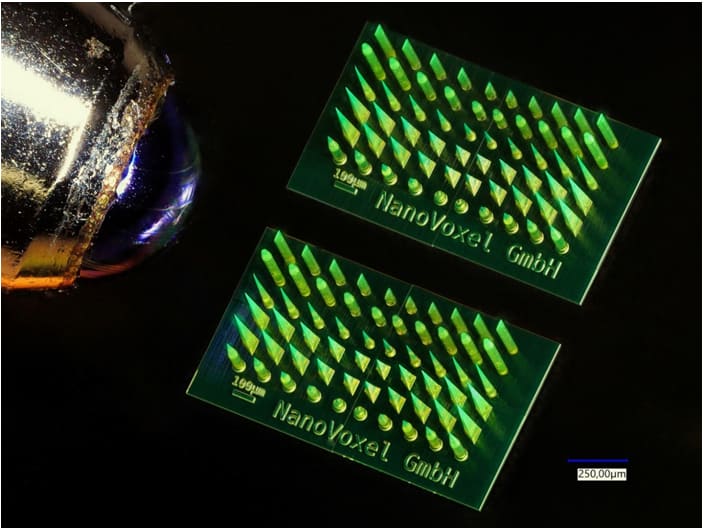
About two decades ago, machine manufacturers, including Wittmann Battenfeld, with its MicroPower 15 t, pioneered specialized injection molding systems. These systems were tailored for precision micro-scale parts, offering industrial modularity and significant economic benefits. Despite this versatility and precision, the bottleneck in micro-part production persisted by their injection cavities, resulting in prolonged lead times of up to 20 weeks. Clients reluctantly accept larger tolerances (± 30 µm), but there's a growing need for shorter lead times, and smaller features, especially in prototype development. The time-consuming precision mold production lingers as the chief bottleneck.
The breakthrough in precision combined with economic efficiency has been achieved in recent years with the 2-photon printer of UpNano, a start-up also based in Vienna and a partner of NanoVoxel. This printer is based on the principle of non-linear absorption of photons, called two-photon polymerization (2PP). A femtosecond laser emits a narrowly focused beam to excite a photosensitive resin. The scanner unit moves the laser beam via Galvano mirrors and lens systems to cure the resin. Like SLA/DLP 3D printing, when the light is absorbed, it triggers a chemical reaction in the resin, causing it to polymerize and solidify at the focal point of the laser beam. However, in a deviation from established 3D printing technologies, 2PP achieves full control of z-dimension polymerization, so holes and cavities are precise and round. The 2PP printing process offers unparalleled precision and resolution to most other manufacturing techniques, enabling the creation of complex 3D micro-structures with sub-micron accuracy, even down to the nanometer range. This makes it ideal for applications requiring particularly intricate detail with high surface quality. A variety of photosensitive resins are available for 2PP printing, including photopolymers and hybrid materials. These materials can be tailored to specific applications and offer a wide range of mechanical, optical, and chemical properties.
Using 2PP printers, micro parts can be printed within hours from a 3D-CAD file with a precision that cannot be achieved by conventional toolmakers, even with the most advanced machinery. Tolerances below 1 µm, structures down to 200 nm, and surface finishes with an average surface roughness better than 10 nm can be produced quickly and economically with this advanced additive manufacturing. Geometries that cannot be produced through injection molding, due to undercuts for example, can be produced quickly with 3D printing. Provisionally, the disadvantage of this technique is its capacity for high volume production, making it uneconomical for parts larger than a few mm.