The limitations of both micro-molding and micro 3D printing pose the question: What changes can expedite lead times, keep high precision, and still maintain high productivity?
To answer this question NanoVoxel GmbH combines the best of both worlds, establishing the union of 2PP printing with micro-injection molding its core business. By using 2PP 3D-printing to quickly produce a high-precision mold for the micro-injection, it replicates the precision and the resolution of 2PP in molded micro-parts with highest efficiency.
NanoVoxel aims to become a one-stop service platform offering flexible and multiple manufacturing solutions and strives to become one of the most innovative companies in the micro manufacturing world. NanoVoxel's multi-disciplinary team of experts combine these different technologies to offer prototypes through to high-volume production as a service provider. This remarkable accomplishment compresses the timeline for structure fabrication into an incredible two-week span.
NanoVoxel has since achieved a breakthrough in the molding of micro-parts that was previously impossible to fulfil, enabling the molding of small, detailed structures with high accuracy and repeatability within tolerances of a few microns. In addition, high-precision 2PP 3D-printing to create mold cavities enables larger parts with single-digit micron features, which would otherwise be time-consuming, expensive, or impossible to produce.
An example of NanoVoxel’s service is the development and manufacturing of an endoscope for the aiEndoscope company: the segments of the endoscope have been initially printed in different design variations at the prototyping stage for geometrical tests and optimization. Upon design validation from the customer, the quickly molded parts were produced and enabled functional and mechanical testing. All the manufacturing process and iterations on this project were completed within 5 weeks.
The capabilities of combining different processes including mastering, casting, and sintering, allow NanoVoxel to create molds with the highest precision, not only from 3D printing materials but also with more robust materials like glass, ceramics, and metals.
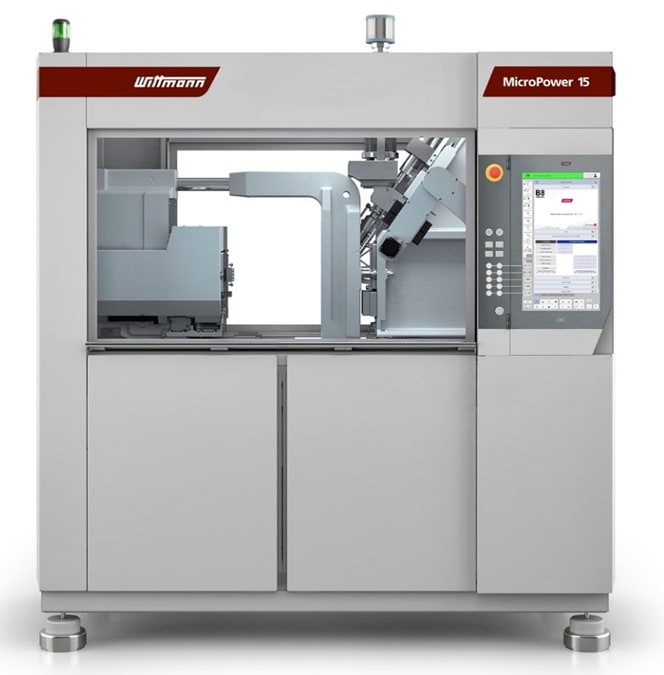
To leverage the highest precision of the molds, NanoVoxel uses the MicroPower 15 t from Wittmann Battenfeld,, a leading manufacturer of injection molding machines and automation solutions. With a clamping force of 150 kN, the machines of the MicroPower series are designed for the economical production of exceedingly small and micro parts with maximum precision and repeat accuracy. A two-stage screw-piston injection unit with a shot volume of 1.2 to 6.0 cm3 injects a thermally homogeneous compound. This makes it possible to produce parts with outstanding precision, extremely stable production, and exceptionally short cycle times. The distinctive design of the machine allows the injection plunger to nearly reach the parting line of the mold. This reduces the mass cushion to a minimum. In addition, the standard version of the machine is already ideally suited for production under clean room conditions: it is designed with an enclosed housing cell. The housing cell offers enough space for the integration of equipment options like a rotary table, robot, material drier, and temperature control units. Robots and peripheral equipment from Wittmann, are specially adapted for this machine. All drive modules of the all-electric drive system, including all mechanical components, are encapsulated in easy-to-clean housings. The extremely well controlled injection of thermally homogeneous thermoplastics in exceptionally small quantities is necessary for successful injection molding of precise and quality consistent mass production of micro-parts.
The combination of 2PP printing and µ-injection molding is not limited to only the high precision rapid tooling process. NanoVoxel GmbH brings a significant addition to the micromanufacturing industry with its capacity to 2PP print directly on parts of different materials manufactured with other processes. This print can be made onto many materials including glass, ceramics, carbon substrates, metals, and plastics. Moreover, the ability to combine varied materials for different functions offers customizability ideal for rapid prototyping, product development, and mass manufacturing. This enables customers to imprint detailed functional features directly onto bulky and larger parts obtained from more efficient processes. Initial applications have been successfully applied in the microfluidics world, where NanoVoxel printed unmoldable features into commercial chips, using their advanced printing process only where needed.
NanoVoxel´s efficiency with the micromanufacturing process unlocks new creative avenues for designers and engineers across diverse industries and revolutionizes the way in which to approach design and fabrication of intricate, customized, and functional micro-scale parts.
Through its commitment to advancing micromanufacturing technologies and re-imagining solutions, NanoVoxel welcomes unconventional part geometry and strives to provide a creative, efficient, and yet simple approach to manufacturing.
Author: Martin Ganz